About us
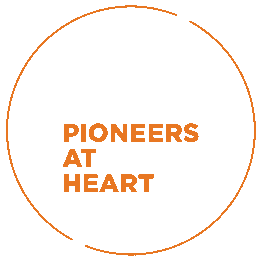
Primetals Technologies, Limited, headquartered in London, United Kingdom, is a pioneer and world leader in the fields of engineering, plant building, and the provision of lifecycle services for the metals industry. The company offers a complete technology, product, and services portfolio that includes integrated electrics and automation, digitalization, and environmental solutions. This covers every step of the iron and steel production chain – from the raw materials to the finished product – and includes the latest rolling solutions for the non-ferrous metals sector. Primetals Technologies is a group company of Mitsubishi Heavy Industries, with around 7,000 employees worldwide.
In Russia, Primetals Technologies is represented by Primetals Technologies Russia Limited Liability Company, consisting of two divisions in Moscow and Yekaterinburg.
The main division in the city of Moscow is engaged in general administration of the Company's work, and also conducts research and analysis of trends in the metallurgy market; develops the potential of the sales market in its region and in the channel for the distribution of the assigned products, solutions, and services; carries out sales and the achievement of the planned rate of return in accordance with the business strategy; provides sales support to the HQ in the Russian market; carries out visa support and provides translation services to the employees of Primetals Technologies Russia LLC and to other affiliated companies.
A separate subdivision in the city of Yekaterinburg is engaged in the design of electrical equipment and automation systems for ferrous and non-ferrous metallurgy. The subdivision's areas of activity also include the supply, assembly, and commissioning of automation systems for production and for machine control.
Over years of work, Primetals Technologies Russia LLC has managed to accumulate a lot of experience in executing both minor and major projects. Our client base comprises around 50 steel plants.
Our simple hierarchy and flexible business model make us constantly available. Around 80% of our employees have over 10 years of professional experience, which is a solid foundation for trust from our clients.
For us, the foremost significance lies in searching for the best solutions and satisfying the expectations of the clients and the market, in generating new ideas and bringing them to life in order to become a consistent leader in our industry.
Competences
Our expertise along the entire value chain
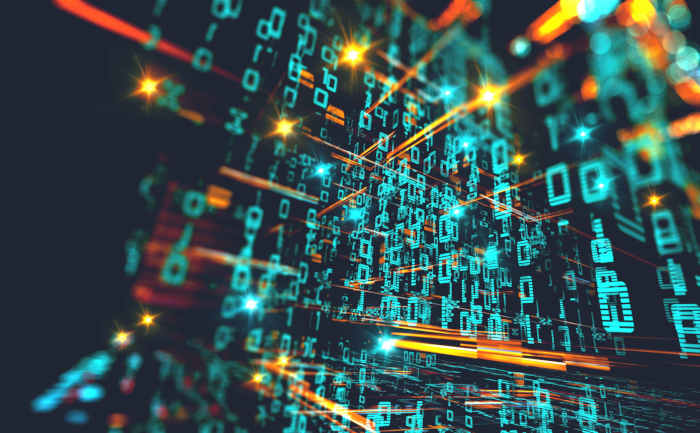
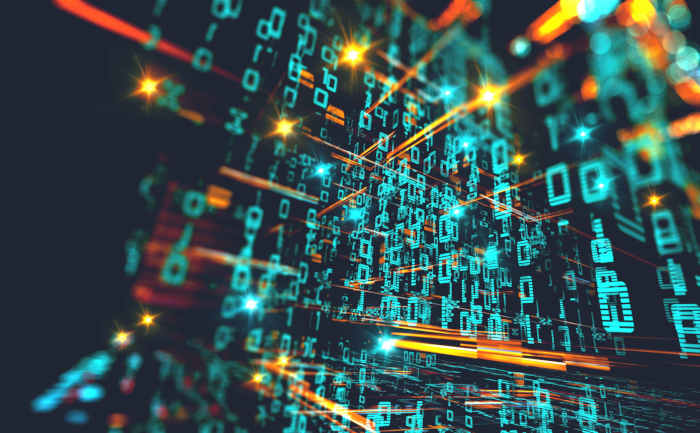
Digitalization — industry 4.0
Metals Orchestra – Instruments for the digital era of steel
Imagine your steel plant as an orchestra where all components work in harmony to manufacture products of highest quality. The “smart” plants of the future contain equipment that is interconnected and can be orchestrated with ease to deliver unparalleled efficiency and reliability.
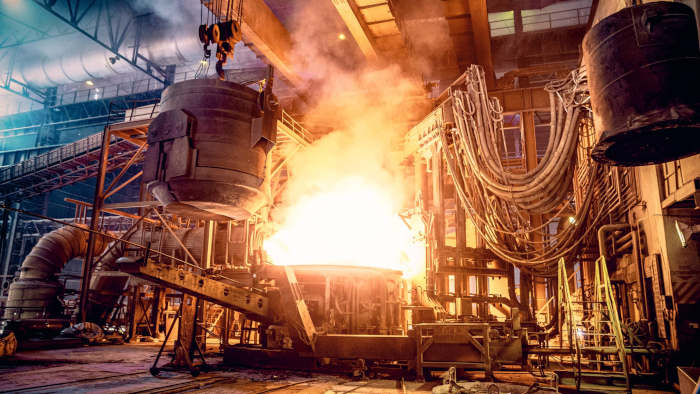
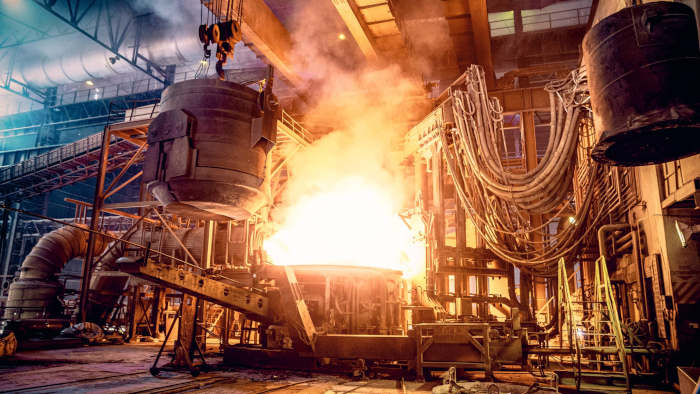
Up to date with electrics and automation
The rising demand for flexible and efficient production processes results in a growing need for integrated electrics and automation solutions during the whole lifetime of metallurgical plants.
Primetals Technologies is the leading supplier of electrics and automation products, solutions and services for the metals industry. The objective is to help our customers optimize availability, profitability and product quality. The Electrical and Automation portfolio spans from basic process automation, power solutions and drives systems to technological process modelling and production planning. In addition we provide modernization packages and Lifecycle Services along the entire production chain. With our global EA setup we realize local support and long term-partnership with our customers to offer specific solutions & services based on our know-how and their individual requirements.
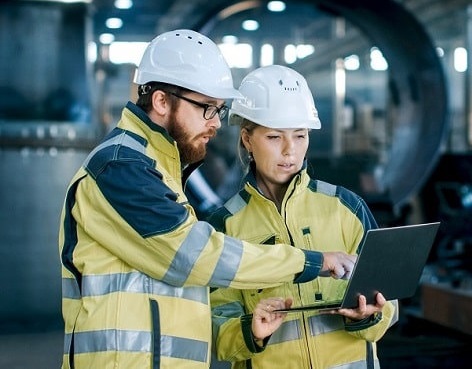
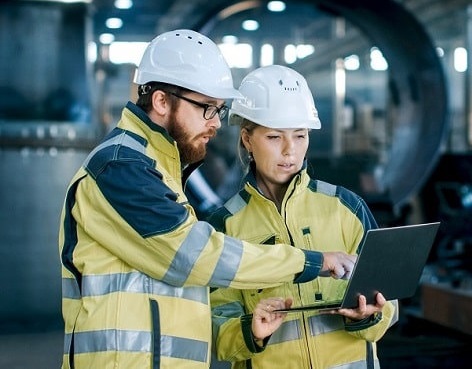
Lifecycle services for steel plants
Reliable technical support, plant upgrades, and proven maintenance services.
Primetals Technologies has the experience required to deliver the full spectrum of technical support, consulting, staff training, and next-level e-services quickly and reliably. We thrive on long-term partnerships with customers, and that’s why we can offer a set of dedicated services that are in place for the entire lifecycle of a steel plant. We are a full-service provider of technical support that includes upgrades, repairs, just-in-time spare parts, and on- and offline maintenance to keep steel plants operating at peak performance. Our service team can help steel plants to slash costs, increase productivity, improve product quality, and raise safety standards.
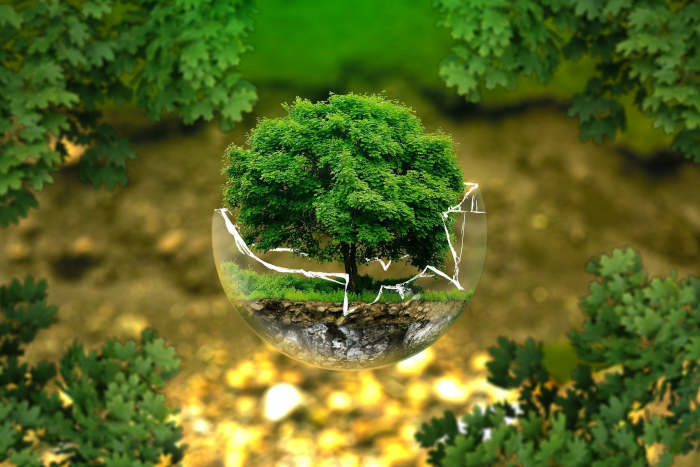
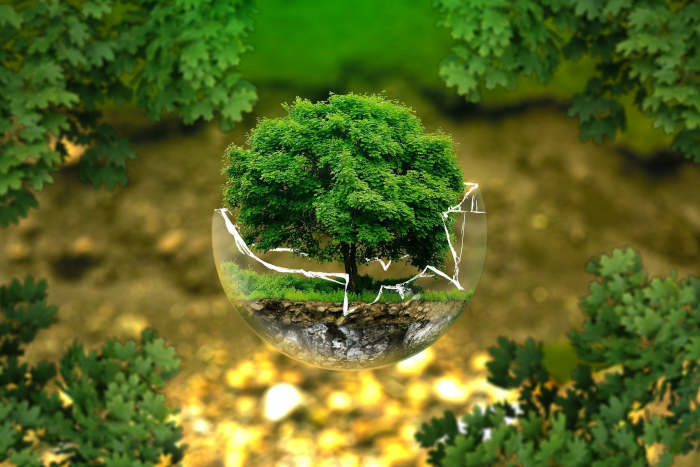
Eco solutions — saving resources, creating value
Due to rising energy prices and stringent environmental regulations, energy efficiency, resource saving and climate protection are becoming more important than ever. Primetals Technologies ECO Solutions offers a wide range of services and technologies to increase energy efficiency, reduce the environmental impact of steel production and to ensure efficient water and by-product management.
Primetals Technologies ECO Solutions provides processes and solutions along the entire iron and steel production chains, which meet the strictest emission regulations and also help producers achieve substantial cost savings. Further, in response to these ecological and economic challenges, Primetals Technologies offers energy-efficient solutions and services along the entire process chain, with a clear objective: saving resources, creating value. The optimized consumption of energy and raw materials, the application of advanced technological processes and the maximum degree of recycling lead to major energy savings, reduced emissions, improved water and by-product management.
Areas of activity
Primetals Technologies Russia LLC offers the following work and services:
- Research and analysis of trends in the metallurgy market;
-
Electrical systems engineering, medium and low voltage:
- Engineering of power distribution systems, control cabinets, and motor control centers, as well as control systems for medium-voltage alternating-current electric drives and low-voltage direct- and alternating-current electric drives.
- Basic engineering (collecting source data and revealing project specificities; establishing the main principles and requirements for carrying out design work), detailed engineering of E&A equipment and power supply / control systems (development of systems for process control and drive control; detail engineering for cabling), assembly engineering using CAD software: EPLAN, AutoCAD, SIGRAPH.
- Preparation of inquiries to design institutes for the development of design documentation for passing the State Expert Review (for projects in Russia).
-
Software engineering for Level 1 automation systems:
- Software engineering for Level 1 automation based on automation tools and software products from Siemens (STEP7, PCS7, WinCC, TIA-portal), as well as from Allen-Bradley, Schneider Electric, Omron, Wonderware.
- Integration and implementation of interfacing between all control systems in use.
- Preparation of instruction manuals for operators and operations personnel (on subjects such as: setup of software and information systems; description of methods for setting up equipment mechanically and electrically).
-
Software engineering for Level 2 automation systems:
- Software engineering for Level 2 automation based on software products C# (.Net), Java, C/C++, Oracle, MS SQL, CLC, VBA
- Data acquisition and storage systems, human-machine interface (HMI), user-friendly output of process parameters, reporting.
- Process modelling, long-term archiving, interfacing with other levels of general shop / general plant automation.
-
Site works:
- Installation supervision and commissioning, both in Russia and abroad.
- Consulting services.
- Training of the Customer's operations and process personnel.
- After-sales support.
-
Creating a digital twin of the production line:
- 3-D modelling of the shop space (arrangement of the lifting equipment and ground transport; transport route; specification of speed and load-related characteristics).
- Main process equipment (XYZ positioning of the main process equipment's points; specification of technical characteristics).
- Control and logistics (creating the process route; logistics simulation software, logistical operations efficiency analysis).
-
Creating hardware and software complexes:
- Automated control system for the technological process of collecting and storing converter gas (Gas holder).
Description of application software:
Application software for converter gas collection and storage system (Gas holder) is designed to control the installation of a gas tank at an industrial enterprise.
The cost of application software is calculated individually. For an accurate cost calculation, you can contact us using the contacts listed on the website.
For download:
Application software documentation (Gas holder)
Set of activities directed at commissioning the software and the APCS¹ information systems includes the following:
- checking the assembly of APCS equipment (PLCs²) in telecommunications cabinets;
- checking the assembly of the electric supply and grounding system;
- assembly and installation of IT equipment in server racks and its commissioning, as well as its connection to the electric network and backup power supply system;
- assembly of local network segment for data exchange between the PLCs (automation Level 1), distributed input / output systems (field level), HMI process visualization system, and the process automation system (Level 2);
- setup of network parameters for organizing communication with the PLCs / HMIs and the PCs / Server of automation Level 2;
- setup of the access rights of information system users;
- setup of special software and databases for organizing storage and distribution (routing) of emergency messages and archive values;
- correction of the existing databases with the setup and filling out of all catalogs;
- software setup, and making changes in the software where required, in accordance with the Software Change Manual, with the aim of optimizing software and eliminating its faults, in accordance with the project solutions (functional description, technical documentation);
- system software setup for operator stations (PCs) and optimization of application software for HMI process visualization;
- training the Customer's personnel within the framework of operating the automated control system (group classes for the Customer's personnel held in accordance with the training plan);
- correction of programs that make up the IS when they produce wrong results under the conditions of being limited by the Technical Assignment and the documentation;
- expansion of functional capabilities and improvement of the characteristics of solutions for specific tasks in accordance with the new or supplemented Technical Assignment.
*APCS – automated process control system
*PLC – programmable logic controller
Documentation
Certificates and licenses:
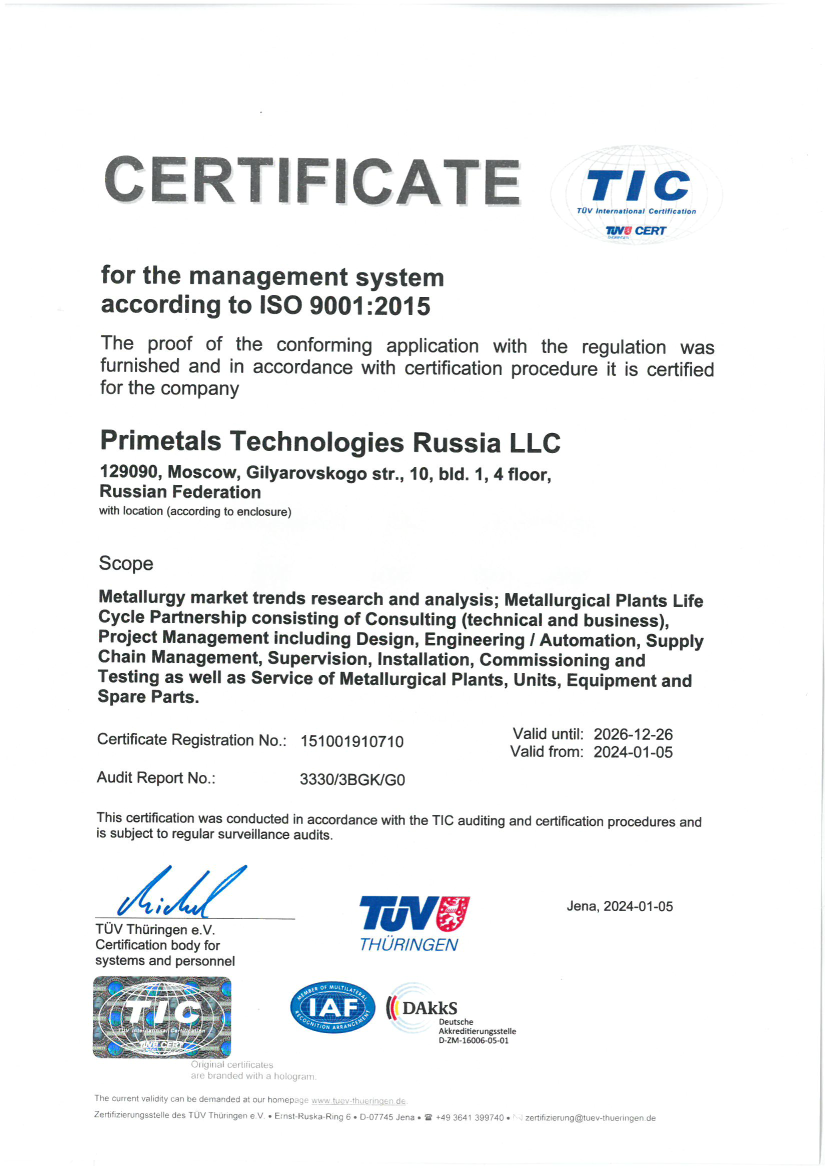
Watch in full
Certificate for the management system according to ISO 9001:2015
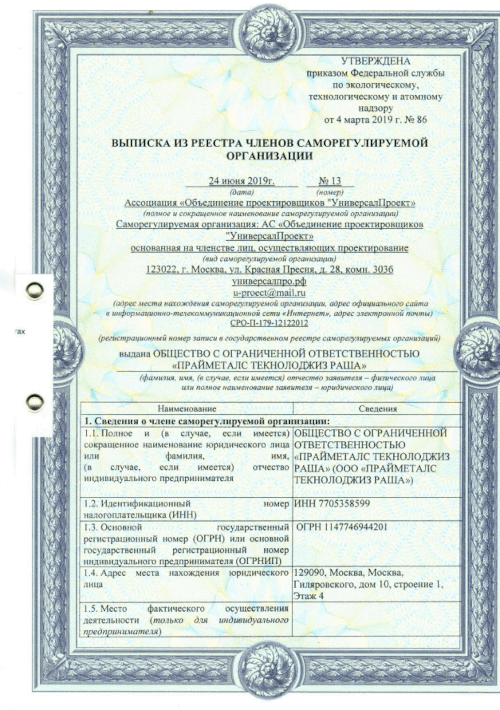
Watch in full
Extract from the register of members of the self-regulatory organization (project group)
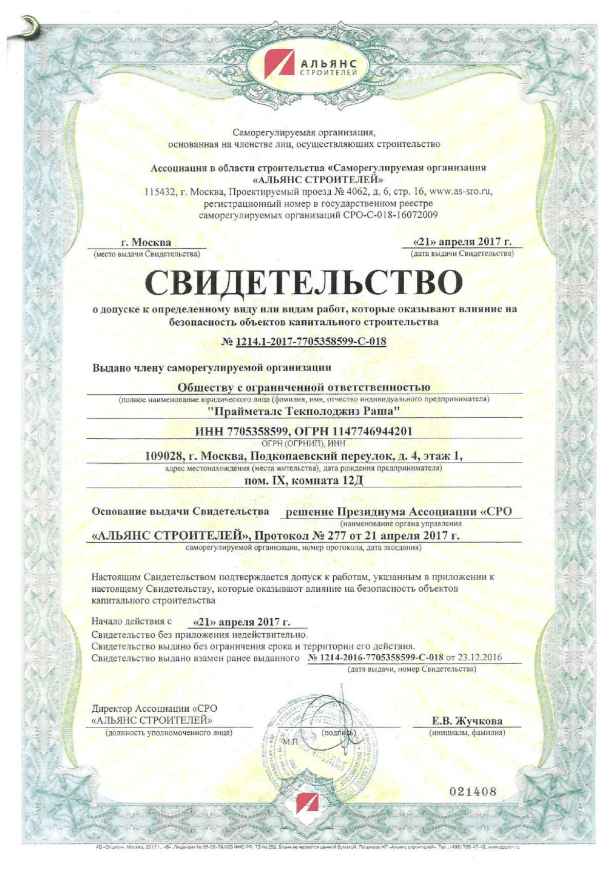
Watch in full
Certificate of admission to certain types of work (construction group)
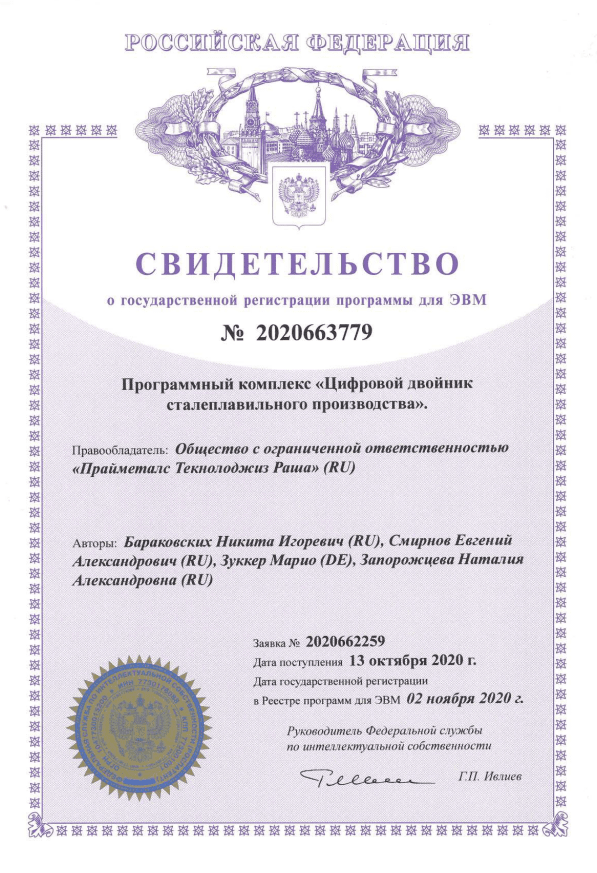
Watch in full
Registration certificate of the "Digital twin for steel-melting" software system
Policies:
News
- Primetals Technologies to supply torch-cutting solution for efficient scrap processing
- Core benefits include zero dust emissions and significantly reduced noise levels
- Enables cutting of bundles of rolled bars
Finnish recycling services provider Konepeikko Oy has awarded Primetals Technologies the contract to supply a new torch-cutting machine for its facilities located at steel producer Ovako Imatra Oy Ab’s premises in Imatra, Finland. This innovative and environmentally friendly solution is part of Primetals Technologies’ latest developments in scrap cutting, and is significantly reducing noise emissions.
Improved Process Efficiency
The scrap cutting machine ensures that Konepeikko Oy is well-positioned to meet the industry’s current and future demand for scrap. According to the World Steel Association, the use of scrap in steelmaking is projected to reach 1,000 million tons annually within a few years. As a result, the need for effective scrap management systems is increasing, aligning with the transition to green steel production.
A highly efficient dedusting system ensures that dust emissions from the cutting process remain well below the limits set by environmental regulations. Additionally, the cutting machine is placed inside a moveable cabin, further reducing noise emissions. This new technology enables Konepeikko Oy to comply with stringent Finnish environmental regulations, which was one of the main influencing factors for its decision, along with improved process efficiency and occupational safety.
Operators control the machine at a safe distance from a desk outside the cutting cabin, supported by a video monitoring system. Predefined cutting programs based on recipes simplify operation and reduce processing times.
Leading Expertise in Torch-Cutting
Konepeikko Oy’s new machine will cut various types of scrap, including billets, blooms, and bundles of rolled bars. Furthermore, the system‘s ability to integrate iron powder into the cutting process allows for cutting of tundish skull, rolling mill rolls, and other hard, high alloy materials.
This advanced technology was developed by experts from former TCT Torch-Cutting Technologies, a Spanish company acquired by Primetals Technologies in August 2023. TCT is renowned for its torch-cutting expertise, offering a wide spectrum of innovative solutions for all kinds of cutting applications in steel plants, rolling mills, forging shops, foundries, and scrapyards.
Konepeikko Oy specializes in recycling, focusing on the acquisition and processing of steel scrap. The company processes more than 50,000 tons of recycled materials annually, and also manages construction waste from demolition sites.
Photo: 3D image of Konepeikko Oy’s scrap-cutting machine from Primetals Technologies. The design accommodates loading from both sides.
- Extensive upgrade of process optimization systems (Level 2) enables production increase from 250,000 to 500,000 tons annually
- Primetals Technologies to execute a carefully crafted three-phase plan for immediate, medium-term, and long-term modernization of Marcegaglia’s minimill in Sheffield, the UK
- Through-Process Optimization study laid foundation for improvement measures
Marcegaglia Stainless Sheffield, based in the UK, has partnered with Primetals Technologies to optimize production processes across its Sheffield minimill. The modernization project aims to double the plant's annual production capacity from 250,000 to 500,000 tons. Several intralogistics systems, process optimization solutions, technology packages, and intelligent sensor systems will be installed at all production units of the meltshop, scrap yard, and the ladle tracking system.
Tailored to Marcegaglia’s Needs
The project is tailored to Marcegaglia's specific requirements, based on a recent Through-Process Optimization (TPO) study conducted by Primetals Technologies. The TPO assessment provided Marcegaglia a comperehensive analysis of the steelmaking plant, identifying bottlenecks and outlining potential improvement measures. A key result of the assessment, the improvement roadmap, highlights recommended actions to achieve a streamlined implementation process.
The TPO study was a key factor in Marcegaglia’s decision to choose Primetals Technologies for this extensive automation upgrade and for the recently awarded electric arc furnace revamping project.
As a first step, Primetals Technologies will install Melt Expert, a fully automated electrode control system for electric arc and ladle furnaces. Mid-term plans include the implementation of process optimization software (Level 2) for the electric arc furnace (EAF), argon-oxygen decarburization (AOD), and ladle furnace (LF) plants, all of which are currently missing from the automation landscape. Long-term plans include the replacement of the electric arc furnace to accommodate the future productivity increase.
A Relationship Beyond System installation
“Marcegaglia chose Primetals Technologies not only for its technical expertise, but also for its commitment to fostering a long-term partnership. This relationship goes beyond system installation to ongoing system updates and development,” said Tom Eades, Engineering Manager at Marcegaglia. The ultimate goal is to increase productivity, which will require introducing an additional production shift. New personnel will be able to gain the necessary knowledge to efficiently run a production unit through Primetals Technologies' new process optimization systems, which provide digitalized knowledge, recommended actions, and training sessions for operators. Marcegaglia intends to start using the standard know-how rules included with all systems, with modifications aligned to operators' best practices as a part of the planned service contract.
Comprehensive Set of Solutions
The scope of supply includes the Scrap Yard Supervisor, which calculates cost-optimized scrap recipes, visualizes process information, and tracks loading processes. Intelligent sensors, such as the Scrap Basket Profile Monitor, monitor specific process steps, identify deviations from standard operating conditions, and notify the operator.
The process optimization solutions EAF Optimizer, AOD Optimizer, and LF Optimizer provide dynamic process control for improved product quality, advanced metallurgical models to meet production-related quality criteria, and detailed calculations of input materials to reduce costs. The Ladle Tracker suggests the most suitable ladle for the upcoming batch, avoiding quality loss caused by residues from previous batches.
Long Stainless Steel of High Quality
Marcegaglia Stainless Sheffield is a global manufacturer of long stainless steel products. The company is known for its ability to provide reliable products of high quality in a wide range of grades, shapes, and sizes. Its stainless steel is a sustainable material with over 90 percent recycled content. Products are melted in Europe using energy sources and raw materials that provide Marcegaglia Stainless’ customers with a carbon footprint lower than industry average.
Marcegaglia will equip all the production units of the minimill meltshop in Sheffield with automation systems from Primetals Technologies.
- Primetals Technologies has installed hot-edge inductors on exit side of an aluminum cold rolling mill, enhancing the rolling capability
- Upgrade has enabled production of high-quality cold-rolled aluminum strip, meeting the demands of the can packaging market
Recently, Primetals Technologies signed the final acceptance certificate (FAC) with aluminum producer Hulamin following the successful installation and commissioning of new hot edge inductors for its cold mill rolling line (S5) in Pietermaritzburg, South Africa. This upgrade effectively addressed the tight edge issues in aluminum strip that occurred during high-speed rolling, leading to improved product quality. The implementation has enabled the production of high-quality coils for demanding markets, such as the can packaging industry.
Improved Product Quality
Primetals Technologies successfully completed the design, procurement, manufacture, supply, and commissioning of the inductor system in just 18 months. The moving induction heating head assembly has been installed on the exit side of the mill, below the exit delivery table. These assemblies are positioned close to the roll surface, just outside of the strip width, effectively counteracting the thermal camber that causes tight edge issues during high-speed rolling.
The hot edge inductors have successfully resolved the tight edge issues by providing additional heat to the work roll at the strip edge, expanding the roll and alleviating tight edges. This improvement has led to better control of the strip edge shape, enabling Hulamin to achieve its key objectives of high product quality and maximum cold mill capacity.
Successful Collaboration
As part of an integrated series of upgrades to Hulamin’s cold rolling system, the implementation of the hot edge inductors has yielded encouraging results. The aluminum producer has observed noticeable improvements in the on-line strip shape performance and continue to further optimize and refine the use of these powerful actuators in its rolling programme.
The way the Hulamin and Primetals Technologies teams collaborated from inception to final testing has been a significant driver to the success of the system. Hulamin’s mill operations team has fully embraced the system and relies on it daily to achieve improved mill productivity with consistent shape performance.
Project Success Sparks Expansion
“Hulamin is extremely pleased with the implementation and the resulting improvement in product quality. Following this success, discussions are ongoing about implementing similar systems on additional mill lines at their site in Pietermaritzburg”, says Calvin Coetzee, Senior Fluids Engineer at Primetals Technologies.
Photo: Inductor system for work rolls from Primetals Technologies.
- Primetals Technologies to supply EAF Ultimate, which will replace two outdated spout-tapping electric arc furnaces
- Active Power Feeder to use direct AC-AC conversion applied at medium voltage – a first for the steel industry
- New power solution provides fast dynamic current control, ensuring efficient energy input to the EAF while minimizing disturbances on the grid
- Startup scheduled for end of 2026
A steel producer based in the U.S.A. has recently awarded Primetals Technologies a contract for the engineering, supply, and startup of a 68-ton EAF Ultimate electric arc furnace (EAF) integrated with Active Power Feeder power supply technology. The order also includes a primary dedusting system, a material handling system, auxiliary equipment, and a complete Level 1 and Level 2 automation system. Startup is scheduled for the end of 2026.
EAF Ultimate – Fully Automated Operation
EAF Ultimate is part of Primetals Technologies’ latest generation of electric steelmaking equipment, characterized by short tap-to-tap times, fully automated operation, and advanced control systems. EAF Ultimate features the modern eccentric bottom-tapping (EBT) system, which eliminates the issue of slag escaping the furnace during tapping, leading to improved final steel quality.
The new equipment will replace two spout-tapping electric arc furnaces and will boast an annual production capacity of 0.75 million tons. The steel producer specializes in medium carbon, high-alloy, and free-cutting steel grades.
Active Power Feeder – Next-Generation EAF Power Supply
The manufacturer has taken a pioneering step by selecting Active Power Feeder technology for this project. With this ground-breaking power supply solution, the company becomes the first steel producer to power an EAF using direct AC-AC conversion utilizing Modular Multilevel Matrix converter (M3C) technology at a medium voltage level, marking a significant advancement in energy efficiency.
The Active Power Feeder solution provides fast dynamic control, resulting in efficient energy input to the EAF while simultaneously minimizing disturbances on the grid.
When combined with Melt Expert, the Active Power Feeder dynamically manages EAF power input and optimizes the melting process. This results in reduced energy consumption, lower electrode usage, decreased production costs, and increased process stability, all while meeting utility regulations. Additionally, the Active Power Feeder system draws symmetrical power and can compensate for the ladle furnace without the need for a separate compensation system.
- Enhanced automation systems result in improved reliability and efficiency
- Project completed ahead of schedule with minimal downtime
Primetals Technologies has upgraded the automation systems at the finishing mill of SAIL Bokaro's hot-strip mill in Bokaro Steel City, Jharkhand, India. This project was completed within 26 months, one month ahead of schedule. The upgrade, featuring advanced Level 1 and Level 2 automation solutions, ensures improved quality, reliability, and efficiency for SAIL Bokaro, a key player in India's steel industry.
Completed Ahead of Schedule
The project involved replacing obsolete automation hardware with state-of-the-art systems, including basic and process automation, flatness and thickness gauges, and a fully virtualized server infrastructure. The scope also covered the adaptation and upgrade of drive interfaces, implementation of new software, and the renewal of measurement technology for profile and flatness.
Despite an ambitious timeline, the project was completed two days ahead of a planned 20-day shutdown, thanks to meticulous planning and close collaboration between the teams of Primetals Technologies and SAIL. Additionally, all relevant mill performance targets were achieved ahead of schedule.
The modernization encompassed automation equipment for the finishing mill, cooling section, down coiler, and coil conveyor. Key technical enhancements included renewing sensors and valve stands for hydraulic adjustments.
Increased Availability
The upgraded automation system offers SAIL Bokaro several benefits, including increased availability and improved technology and functionality. The modern human-machine interface (HMI) and diagnostics system supports operators and maintenance staff with advanced and rapid troubleshooting capabilities, contributing to reduced downtime at the finishing mill. The new systems are operated on virtualized servers, ensuring smooth operations and enhanced production quality.
A Leading Indian Steel Producer
SAIL Bokaro, a unit of the Steel Authority of India Limited (SAIL), is one of the largest steel plants in India. Established in the 1960s, the Bokaro steel plant has become a cornerstone of India's steel production. The plant specializes in producing flat products such as hot rolled coils, hot rolled plates, cold rolled coils, and galvanized sheets, serving various industries including automotive, liquefied petroleum gas (LPG) cylinder production, and pipe and tube manufacturing.
Cooling section at SAIL Bokaro’s hot-strip mill. Primetals Technologies’ modernization encompassed automation equipment for the finishing mill, cooling section, down coiler, and coil conveyor.
- Primetals Technologies receives final acceptance certificate for revamp of billet caster
- Caster fully implemented during exceptionally short shutdown period of six weeks
- Retractable oscillators result in increased productivity
- Optimization of LevCon parameters leads to a 34 percent increase in mold level stability
Italian steel producer Feralpi Siderurgica (part of Feralpi Group) has granted the final acceptance certificate (FAC) to Primetals Technologies for a revamp of its 6-strand billet caster at the steel plant in Lonato del Garda, Italy. The revamped caster was implemented within just six weeks during the planned summer shutdown of 2023. The project took only 12 months from contract signing to the first cast – usually, similar projects take at least 1.5 years until completion.
The extraordinarily swift implementation was achieved through tailored design features specific to Feralpi’s needs, along with close collaboration and knowledge sharing between Feralpi’s and Primetals Technologies’ technicians. Primetals Technologies engineered the caster bow as a single piece for all six strands and preassembled the equipment before transportation to Feralpi’s location. Moreover, the molds and retractable oscillators were designed and built as a single unit, contributing to a smooth on-site implementation.
Mold Changes During Casting Sequences
Primetals Technologies installed retractable oscillators as part of the revamp, resulting in increased productivity. For conventional billet caster designs, changing a mold requires a complete production stop on all strands. However, the retractable oscillators are mounted on mobile carriages, allowing each oscillator to be detached individually for mold changes. This configuration allows operators to exchange molds on one strand while keeping the other strands operational.
Improved Center Quality of Billets
Primetals Technologies’ scope of supply included key mechanical equipment such as the caster bow, retractable oscillators, strand guiding units, drive adoption of the withdrawal strand unit (WSU), and a pinch roll. The comprehensive electrics and automation solution for the mold/oscillator, including the LevCon Autostart function, and implementation services, rounds off the scope.
Increased Mold Level Stability
As part of the project, Primetals Technologies’ automation experts collaborated with Feralpi engineers to identify optimization areas that could enhance production performance. The evaluation revealed that response times for the withdrawal drives could be improved. The team implemented a new set of LevCon parameters based on a numerical optimization approach.
The new state-of-the-art LevCon function for open stream casting enables improved mold level control, resulting in an average 34 percent improvement for the standard deviation of the mold level, i.e. the value indicating mold level stability. Feralpi has expressed satisfaction with the project, noting that the new technology has set a new standard for precise mold-level control. LevCon’s Autostart function has also become part of Feralpi’s ongoing operations, minimizing the risk of breakouts.
Feralpi Group, which controls several international companies, is a leading supplier to the European construction industry with an annual production capacity of 2.45 million tons. Known for its commitment to circular economy initiatives, Feralpi produces 98.6% of its steel using recycled and recovered materials or by-products. The group operates several subsidiaries in Italy and has production and sales locations in Europe and North Africa. Founded in 1968, Feralpi Siderurgica is the oldest company in the Feralpi Group and is a key European supplier of reinforcing steel, wire rod, reinforcement meshes, and related products.
Key facts: 6-strand billet caster at Feralpi Lonato
Dimension of billets
140 to 160 millimeters
Casting speed
Up to 3.25 meters per minute
- Primetals Technologies secures ten-year contract in Brazil and five-year contract in Mexico
- Covers maintenance services of multiple continuous casters and related equipment
- Benefits for the steel producer include increased productivity and more reliable operations
Primetals Technologies recently renewed two contracts with a leading steel producer in the Americas for maintenance services of several continuous casters. The scope of services includes maintenance work for oscillators, molds, benders, segments, and runout rollers.
A Long-Standing Partnership
The steel producer, a prominent company in the Americas, operates multiple production centers across the region and is manufacturing a wide range of high-complexity steel products for major industries and markets.
In Brazil, Primetals Technologies has been providing caster maintenance services for this reputable company for more than a decade. Over this period, the partners have developed a close relationship based on trust, reinforced by the high level of responsiveness and performance of the Primetals Technologies team. To further improve the quality and availability of its service offerings, Primetals Technologies will invest in new machinery for its workshops in Santa Cruz, Brazil.
In Mexico, off-line continuous caster maintenance has been executed by Primetals Technologies over the last five years. This has included, along the standard service, also the optimization and the implementation of innovative new technology solutions for a machine installed about 30 years ago.
The newly extended maintenance contract includes specialized services such as copper plate refurbishment and the on-site presence of maintenance personnel with expert knowledge for both assessment and the implementation of state-of-the-art service solutions.
Increased Productivity
The ongoing services from Primetals Technologies, along with the planned investments, will ultimately result in several improvements related to overall plant performance, such as increased equipment lifespan and reduced downtime. This, in turn, will benefit the customer by increasing productivity and enhancing reliability, while reducing operational risk.
“As a long-standing partner, I am pleased to announce our customer’s decision to renew our contracts in Brazil and Mexico. This renewal is a clear endorsement of the exceptional quality and reliability of our maintenance services,” says Eberhard Karnitsch-Einberger, Head of Metallurgical Services at Primetals Technologies. “Our commitment to excellence and continuous investment in improving our services have significantly contributed to our operational success, enabling our partner to cast higher-quality steel. We are confident that this sustained collaboration will keep both our partner and us at the forefront of the industry, driving innovation and excellence in all our actions.”
The new Primetals Technologies workshop located in Santa Cruz, Brazil.
- Substation from Primetals Technologies to function as link between the power grid and the electric arc furnace (EAF) plant
- Startup scheduled for August 2026
Saarstahl has placed a significant order with Primetals Technologies for a new substation to be located at its plant in Völklingen, Germany. The new power supply solution will serve as the link between the power grid and a new, not yet implemented, electric arc furnace plant. Startup is planned for August 2026.
Primetals Technologies will design, supply, and implement a complete substation for transforming voltage from 110 to 35 or 10.5 kilovolt (kV). The solution will feature a 110 kV gas-insulated switchgear, three 200 megavolt-amperes (MVA) transformers, and one 40 MVA transformer. The equipment also comprises a 35 kV gas-insulated switchgear as well as a 10.5 kV air-insulated switchgear. High-level supervision of the substation will be executed by a SCADA control system.
A Long-Lasting Collaboration
In the first part of the project, Primetals Technologies conducted a comprehensive study to outline the optimal substation technology for Saarstahl. The steel producer’s decision to work with Primetals Technologies for this technical solution and related services reflects the longstanding relationship between the two companies, as well as the benefit of having Primetals Technologies’ Saarbrücken office being in close proximity to the plant.
This large order also highlights Primetals Technologies’ ability to execute major energy supply projects alongside conventional plant engineering and building projects, thanks to the knowledge and expertise gained through its history of supplying similar large energy systems for customers worldwide.
Dillinger and Saarstahl are two leading European steel producers, and steel products from the companies are used in demanding applications such as the headquarters of French daily newspaper Le Monde and London’s tallest building, Twentytwo, as well as in the safe tracks of European high-speed trains and in the majority of cars manufactured in Europe. With their ambitious Pure Steel + program, Saarstahl and Dillinger primarily aim to achieve carbon neutrality by 2045, having secured funding of 2.6 billion euros in total.
Recently, Dillinger and its subsidiary ROGESA signed contracts with Primetals Technologies for the supply of a new production complex, which includes a DRI plant contracted along with Midrex Technologies and an EAF Ultimate electric arc furnace plant, including two twin ladle furnaces.
In the photo:
The area at Saarstahl’s site in Völklingen, Germany where the large substation from Primetals Technologies will be constructed. Copyright: Uwe Braun, SHS - Stahl-Holding-Saar
- Both wire rod mill outlet and bar-in-coil line expand rolling mill capacity for large size products and low temperature thermomechanical rolling
- New eDrive mini-finishing mill increases efficiency through integrated single-family rolling
- Bar-in-coil outlet expands size range to further enhance Baoshan’s market presence
Primetals Technologies has recently completed an installation at Baoshan Iron and Steel in Shanghai, China, for a new combination mill featuring both a wire rod mill outlet and bar-in-coil line to produce 600,000 tons per year of wire rod and bar products. This installation is Baoshan’s first greenfield long rolling investment since the original mill installation in 1998. The new mill is specifically designed to increase rolling mill capacity and expand size range with the wire rod mill outlet handling 7.5-to-29-millimeter rod and the bar-in-coil line handling 8-to-50-millimeter bar.
A New Technology for Increased Rolling Capacity
To reduce downtime, Primetals Technologies utilized four eDrive mini-finishing mills with 250 millimeter ultra heavy-duty roll housings for integrated single-family rolling from a standardized mill train. eDrive is one of Primetals Technologies’ newest long rolling solutions. Its purpose is to expand the already extensive capabilities of the company’s line of long rolling mill products by increasing load-carrying capacity, reducing long-term costs, enabling low temperature thermomechanical rolling, using quick-change roll units, and more.
The project scope included equipment supply, engineering, and site supervision services as an open consortium between Baowu Steel Group and Primetals Technologies. The full list of equipment included four eDrive mini-finishing mills, guide optics, a pinch roll and laying head, the latest high-speed pouring reels, as well as a mechatronics package comprising of the mechanical software necessary for this key equipment.
Dedicated Customer Support
In a letter of appreciation, Tang Jinsong, Director of Long Rolling at Baosteel, expressed his gratitude to Primetals Technologies saying, “During the commissioning period, we received the highly specialized technical support from Primetals Technologies’ site team including rolling process, fluids, and mechanical supervision personnel, as well as careful and personal service from the aftermarket service team. We are deeply satisfied with this and would like to express our sincere gratitude.”
“Primetals Technologies high-speed rod mill eDrive and bar-in-coil technology has been well received and the progress of the project has been highly praised by all parties.”
Baoshan Iron and Steel, a subsidiary of Baowu Steel Group located in Shanghai, PRC, is a comprehensive steel service company specializing in the processing, sales, and technical services of stainless steel and carbon steel alloys, including high quality wire rod products since the late 1990s.
Hot coil during bar-in-coil outlet commissioning.
- Next-level production flexibility in terms of raw material utilization
- Significantly reduced production costs
Chinese special steel producer Huaigang Special Steel, a part of the Jiangsu Shagang Group, has recently granted the final acceptance certificate (FAC) to Primetals Technologies for an 80-ton EAF Quantum electric arc furnace, implemented at a site in Huai'an, Jiangsu province. The first heat was produced in January 2024, just five months after Primetals Technologies and Huaigang Special Steel commenced on-site installation works.
Tap-to-Tap Times of 32 Minutes
This EAF Quantum offers remarkable production flexibility, achieving single heats with tap-to-tap times of 32 minutes. In July, Huaigang operated the furnace on 25 percent hot metal and 75 percent scrap at a power consumption of 240 kilowatt-hours (kWh) per ton and an oxygen consumption of 23 to 25 cubic meters per ton. The following month, Huaigang switched to 100 percent scrap. Additionally, they have used a mix of 30 percent hot metal and 70 percent scrap, achieving power consumption figures of less than 230 kWh per ton. Huaigang also has the option to utilize 30 to 40 percent hot metal during the charging process.
Primetals Technologies has supplied Huaigang with key mechanical and electrics process equipment, as well as a Level 1 automation system, an automated charging process, automation systems for oxygen injection and sand filling, and a Level 2 automation system.
Outstanding Power Consumption Figures
In 2021, Jiangsu Shagang Group ordered its first EAF Quantum from Primetals Technologies. Positive experiences with this project contributed to their decision to order a second EAF Quantum in 2022. Huaigang Special Steel’s existing line produces 3.2 million tons of special steel annually. Focused on high-end special steels, such as spring steel and bearing steel, Huaigang is a leader in China’s special steel market.
The flexible application of raw materials and the EAF Quantum’s high melting efficiency ensure the production of high-quality special steel products, further reducing melting power consumption to less than 230 kWh per ton for single heats and significantly shortening melting times. Compared with conventional EAF plants, production costs are reduced by more than 20 percent.
Exhaust Gas Used to Preheat Scrap
One of the most significant differences between conventional EAF plants and the EAF Quantum is the scrap preheating process. The EAF Quantum features a trapezoidal shaft and a scrap retention system. This design optimizes scrap distribution and allows exhaust gas to preheat scrap. As a result, the EAF Quantum requires less time and energy to melt scrap, reducing power consumption and increasing productivity due to shorter processing times.
Picture of the first heat at Huaigang’s EAF Quantum supplied by Primetals Technologies.
- Primetals Technologies to supply and implement DRI plant and EAF Ultimate
- New green steel production complex with an annual capacity of 2 million tons
- DRI plant to be provided in collaboration with Midrex Technologies
- Represents significant step in Dillinger’s and ROGESA’s conversion to decarbonized production
On October 11, German steel producer Dillinger and its subsidiary ROGESA signed contracts with Primetals Technologies for the supply of a new production complex, which includes a DRI plant, contracted along with Midrex Technologies, and an EAF Ultimate electric arc furnace plant including two twin ladle furnaces. These solutions from Primetals Technologies will support Dillinger and ROGESA to meet their goal of reducing CO2 emissions by 4.8 million tons per year within six years.
Dillinger and ROGESA, as part of the SHS Group (SHS – Stahl-Holding-Saar), have launched an ambitious green steel transformation project to replace the current blast furnace-based production route in Dillingen, Germany. Having a single supplier for the complete range of ironmaking and steelmaking facilities comes with several benefits for Dillinger and ROGESA, particularly in terms of implementation and tailored design features to accommodate for plant installations alongside existing equipment. Dillinger and ROGESA chose Primetals Technologies based on its leading technological solutions and strong references for both DRI plants and EAF technology.
“This partnership with Primetals Technologies represents an important building block on the way to climate friendly steel production here in Germany, “ said Dr. Peter Maagh, Chief Technical Officer at Dillinger. “We are convinced that we can successfully launch our Power4Steel decarbonization project on schedule with such an experienced and reliable partner.“
DRI Plant for Flexible Transition to Hydrogen
The new direct reduction plant will produce hot direct reduced iron (HDRI) and cold DRI (CDRI) with an annual capacity of 2 million tons. A consortium of Midrex and Primetals Technologies will handle the engineering and supply of both mechanical as well as electrics and automation equipment. This includes a material handling system, a water treatment plant, auxiliary equipment, and training and advisory services. Primetals Technologies will also provide a complete basic (Level 1) and process optimization (Level 2) system featuring the DRIpax expert system, which ensures consistent high quality of the produced DRI.
“The transition to green steel production will not happen overnight, we will see a step-by-step process towards carbon neutrality,” said Andreas Viehböck, Head of Upstream Technologies at Primetals Technologies. “With this investment, Dillinger and ROGESA are set to reach their mid- to long term goals in terms of decarbonization. The solutions from Primetals Technologies and Midrex will allow them to ramp up the use of hydrogen gradually while adapting to a changing energy landscape. We are very happy to support them on this endeavour and beyond.”
The MIDREX Flex technology is designed to operate at different ratios of natural gas and hydrogen, up to 100 percent hydrogen. Initially, the plant will be operated with a mix of natural gas and hydrogen, allowing for a carbon footprint reduction of more than 50 percent compared to blast furnace based ironmaking. The MIDREX Flex plant will be implemented with hydrogen-ready equipment and piping, such as three stages of process gas compressors. Moreover, it features a hot transport conveyor to utilize the valuable heat of the HDRI for direct charging into the electric arc furnace at the Dillingen site. A DRI cooling solution will enable the transport of CDRI.
“The decision by Dillinger and ROGESA for MIDREX Flex technology allows them to transition to hydrogen-based ironmaking at the pace that matches the availability of sufficient gas supply while reducing their current CO2 emissions significantly,” K.C. Woody, Midrex President and CEO, said. “DRI-based steelmaking provides a pathway to a sustainable future, both economically and environmentally, and our technology solutions offer the flexibility and performance to turn promise into success.”
EAF Ultimate – High Flexibility and Fully Automated Operation
The EAF Ultimate represents Primetals Technologies’ latest development in electric steelmaking. The fully automated plant will ensure short tap-to-tap times and reduced consumption. It offers high flexibility in terms of raw material input and the production of a wide range of steel grades.
Primetals Technologies extensive scope of supply for the new meltshop includes a 195-ton furnace with a 9.6-meter furnace diameter and a powerful 300 megavolt-amperes (MVA) transformer, the LiquiRob robotics system for enhanced safety operations, two 195-ton twin ladle furnaces (LF), a material handling system, primary, secondary, and auxiliary dedusting systems for the EAF plant, a waste heat recovery system, and a water treatment plant. The heat recovery system converts waste heat into steam, which will be reused in other production units.
The EAF Ultimate will feature advanced Level 1 and Level 2 automation systems, including the EAF Controller and EAF Optimizer, enabling both closed-loop control of the furnace for a precise fulfilment of the desired product quality and detailed production planning.
Comprehensive Digitalization Solutions
A swift implementation of learnings and evaluations will play a key role as the new production complex is put into operation, which places high demands on the automation systems. Both plants will be equipped with the latest digitalization solutions from Primetals Technologies. The condition-monitoring system Asset Life Expert (ALEX) identify potential incidents before they occur to support predictive maintenance, which together with the Lomas off-gas analysis system will enhance process-efficiency and safety.
Primetals Technologies’ virtual plant solutions for both the DRI and the EAF plant will allow testing of software and operator training before startup and throughout the entire lifecycle of the plant, ensuring a smooth ramp-up of production. Moreover, the scrap yard will be equipped with AI-based sensor systems, allowing fully automated operation of the scrap yard.
The Melt Expert electrode control system will be installed at both the EAF plant and the LFs, offering productivity gains and cost-savings related to reduced consumption.
Leading Supplier of Decarbonization Technologies
Primetals Technologies and its consortium partner DSD Montagetechnik, part of the German DSD Steel Group, will provide advisory services for the construction and implementation of the DRI plant and EAF equipment.
Dillinger and ROGESA’s new production complex is Primetals Technologies’ latest major decarbonization project. Recently, Oslo-based Blastr selected the company as its technology partner for new green steel production facilities in Finland. This, along with projects for voestalpine in Austria, Salzgitter in Germany, and Marcegaglia in the UK for comprehensive EAF projects, solidifies Primetals Technologies’ role as leading supplier of decarbonization solutions.
Carbon Neutrality by 2045
SHS Group, consisting of several leading companies in the steel market, aims to achieve carbon neutrality by 2045 through its ambitious Power4Steel program. Steel products from SHS Group companies are used in demanding applications, such as the headquarters of French daily newspaper Le Monde and London’s tallest building, Twentytwo, as well as in the safe tracks of European high-speed trains and in the majority of cars manufactured in Europe.
SHS Group has obtained funding for its green transition from the German state and the state of Saarland. The fundings are approved by the European Union.
The DRI plant will be provided by a consortium of Midrex and Primetals Technologies.
EAF Ultimate electric arc furnace plant from Primetals Technologies.
- Primetals Technologies patented bend-resistant staves ensure a longer lifetime
- Wear-resistant hexagonal inserts lower operating costs and carbon emissions through reduced coke usage
Blast Furnace No.1 at Dragon Steel Corporation’s (DSC) plant in Taichung, Taiwan, was originally designed, supplied, built, and commissioned by Primetals Technologies in 2010. Having exceeded its capacity with a record performance of 15 percent above design, the furnace will be taken offline in 2025 for a revamp in preparation for another successful campaign.
As part of the revamp, DSC is replacing the full set of staves to the original design with the addition of ten staves containing Primetals Technologies’ patented wear-resistant copper staves and anti-bending solution in key areas of the furnace.
Continued Reliable Operation
The latest stave designs from Primetals Technologies will support the continued reliable operation of the furnace cooling system, extend the campaign life, and minimize maintenance. The introduction of the wear-resistant technology also reduces operating costs and carbon emissions by lowering coke consumption.
Primetals Technologies will design and supply the bend and wear-resistant staves directly to the Taichung site. Blast furnace experts from Primetals Technologies will provide advisory services for installation and performance testing.
Leading Integrated Steel Manufacturer
Dragon Steel Corporation became a fully-owned subsidiary of China Steel Corporation in 2008. Located in Taichung, Taiwan, DSC is the country’s only wholly integrated steel plant, equipped with both an electric arc furnace and two blast furnaces. Its main facilities incorporate the latest highly efficient and environmentally friendly designs.
The two blast furnaces at the site have a combined annual capacity of 5 million metric tons and provide feedstock for the adjacent steelmaking facility. Steel produced at Taichung includes general carbon steel, structural steel, and high-strength low-alloy steel. The site also produces general structural steel with the largest hot-rolled thickness and width in the CSC Group.
Primetals Technologies Copper Staves to be installed on Dragon Steel Corporation, Taichung Blast Furnace No.1 (Image authorized by DSC).
- Primetals Technologies to modernize Level 1 and Level 2 automation systems
- Ulsan Aluminum to benefit from increased IT security and future-proof operations
- Implementation planned for October 2025
Primetals Technologies has recently received an order from South Korean aluminum producer Ulsan Aluminum for a comprehensive upgrade of the automation systems at its 3-stand hot finishing mill in Ulsan, South Korea.
Modernization of Level 1 and 2 Automation
The project scope includes system upgrades of both the Level 1 and Level 2 automation systems, virtualization of all servers, and modernization of the process automation’s human-machine interface (HMI) system.
The main benefits for Ulsan Aluminum are significantly increased IT security, reduced OPEX-related costs, and future-proof operations. This upgrade will enable Ulsan Aluminum to smoothly integrate digital assistants and other digitalization solutions.
Primetals Technologies originally supplied the hot rolling mill in 2013. The mill was added to an existing hot reversing twin coiling mill to increase throughput, as part of plans to expand into automotive sheet production in the Asian market. The entry thicknesses range from 25 to 60 millimeters, while exit thicknesses vary from 1.8 to 6 millimeters.
Improved Product Quality
All systems will be operated on virtual servers, which reduces maintenance needs and enables fast scaling of digital services. As a result of the modernization, Ulsan Aluminum can expect improved product quality and increased productivity. Plant shutdown and implementation is scheduled for September to October 2025.
Formed in 2017, Ulsan Aluminum is a joint venture of Novelis and Kobe Steel. The company is a leading supplier of aluminum flat-rolled products to various market segments, including automotive, beverage cans, and specialty aluminum applications. The plant in Ulsan boasts an annual capacity of 400 000 tons.
- New equipment ensures increased lifetime and reduced maintenance needs
- Tilting drive fully tested before shipment, resulting in streamlined on-site assembly
- Emergency drives secure full availability, even in case of power outages
South Korean steel producer POSCO has chosen Primetals Technologies to supply a new tilting drive for LD converter (BOF) No. 3-2 at its plant in Pohang. The new equipment went into operation at the end of June 2024. Primetals Technologies was responsible for engineering, manufacturing, supply of equipment, advisory services, and training of on-site personnel.
Shipped as One 110-Ton Piece
The Primetals Technologies team chose to manufacture, test, and inspect the tilting drive at a workshop in Milan, Italy, before transporting it to the Genoa harbour and shipping it as one 110-ton piece to South Korea. As a result, on-site pre-assembly times were significantly reduced.
The new tilting drive features Primetals Technologies’ optimized gear-tooth profile, hardened gears, and increased housing stiffness, all of which allow for higher torques. Additionally, POSCO will benefit from a reduced need for maintenance and increased equipment lifetime compared to the previous implementation. Primetals Technologies also installed pneumatic emergency drives to ensure full availability of the tilting drive, even in case of power outages and other unforeseen events.
A Strong, Collaborative Relationship
POSCO and Primetals Technologies have built a long and successful relationship, showcased by numerous converter projects over the years, some of which have included special converters such as KOBM for improved steel quality. In 2017, Primetals Technologies supplied another tilting drive for LD converter (BOF) No. 1 at the Gwangyang plant.
With an annual capacity of 42 million tons, POSCO exports a wide range of steel products, including hot-rolled sheets, plate, wire rod, cold-rolled sheets, galvanized sheets, and stainless steel, to numerous countries across the globe. POSCO supplies steel products to major industries, including automotive, shipbuilding, construction, energy, and home appliances.
- New five-year cost-per-ton maintenance contract
- Repair and maintenance of continuous caster equipment and components
- Process improvements to enhance equipment performance and longevity
- Work to be performed at a nearby 40,000-square-foot facility operated by Primetals Technologies
Primetals Technologies has secured a five-year cost-per-ton maintenance contract from Outokumpu Stainless USA, a leader in stainless steel manufacturing. The company will be responsible for the repair and maintenance of Outokumpu’s single-strand continuous casting machine in Calvert, Alabama.
Committed to Process Improvements
This contract marks a significant shift from previous maintenance work. Primetals Technologies will apply its in-depth knowledge of the original equipment and introduce future process improvements. The company is committed to enhancing the performance and longevity of the continuous caster, which it supplied to Outokumpu in 2012. This includes implementing the latest advancements in mold coating and roll overlay technologies.
The maintenance work will be relocated to a nearby 40,000-square-foot facility in Calvert, operated by Primetals Technologies. This move will streamline maintenance operations and provide Outokumpu with additional space in its meltshop for other production activities. Throughout the transition, there will be no disruption to Outokumpu’s production in Calvert or the operation of the continuous casting machine.
Securing this contract, along with a recent caster maintenance agreement from ArcelorMittal Nippon Steel (AM/NS) Calvert, further strengthens Primetals Technologies’ upstream and downstream service offerings in the United States.
Comprehensive Maintenance Scope
The contract covers a wide range of maintenance activities for continuous caster equipment, ensuring optimal equipment performance and longevity. This includes the repair and servicing of molds, oscillators, as well as the bender, bow, straightener, and horizontal segments. Additionally, Primetals Technologies has been tasked with the upkeep of caster rolls (both new and reconditioned), spindles, table rollers, table drive shafts, and all spart-part management.
Primetals Technologies will also apply its innovative Hiper Coat technology to the mold coppers, which offers variable hardness to extend the life of these components. Similarly, its proprietary overlay technology will enhance the performance and durability of the caster rolls. The contract also entails bi-annual strand alignment and reporting, labor and supervision for core equipment maintenance, and operational expert support services.
Access to Advanced Technology
Another advantage that Primetals Technologies offers is the option for its customers to access remote assistance through its advanced operations-management platform called Through-Process Optimization. Additionally, the m.space e-services platform allows operators to order spare parts online, access helpful training sessions, and centralize plant documentation.
Furthermore, the Maintenance and Asset Technology (MAT) platform offers a suite of tools for real-time tracking of mold copper and roll fleets. Developed by Primetals Technologies, MAT’s predictive maintenance scheduling employs reliability-centered maintenance strategies to address failure modes and optimize asset lifetime. MAT also includes graphical work order tracking, forecasting to boost overall productivity, and a KPI dashboard for insightful reporting. Designed for portability, MAT can be operated on tablets, ensuring on-site and offline accessibility.
About Outokumpu
Outokumpu is accelerating the green transition as the global leader in sustainable stainless steel. Its business is based on the circular economy: Outokumpu’s products are made from 95 percent recycled materials, which it then turns into fully recyclable stainless steel. This steel is utilized in various applications across society, including infrastructure, mobility, and household appliances. In the US, Outokumpu operates America’s most advanced stainless-steel mill in Calvert, Alabama. With an extensive range of products and industry-leading technical support and services, Outokumpu is the second-largest producer of sustainable stainless steel in the United States. Learn more at: www.outokumpu.com
- Primetals Technologies to modernize spout-type electric arc furnace (EAF) plant and its dedusting system
- Marcegaglia’s Sheffield meltshop will see efficiency and environmental improvements
- Implementation scheduled for mid-2026
Founded by Steno Marcegaglia in 1959, Marcegaglia Group is a leading player in the global steel industry, specialized in steel product transformation. In 2023, Marcegaglia Group realized the long-held vision of its founder by entering liquid steel production through the acquisition of Outokumpu’s stainless steel long product division, including the Sheffield Meltshop, which focuses on producing stainless steel billets, blooms, and slabs.
In August 2024, Marcegaglia tasked Primetals Technologies with a comprehensive modernization of the existing spout-type electric arc furnace (EAF) plant and its dedusting system. The order came after a recent study executed by Primetals Technologies, which was focused on optimizing measures for the meltshop aimed at increased productivity.
Efficiency And Environmental Improvements
Sheffield is historically significant as the birthplace of stainless steel production technology, this is the city where English metallurgist Harry Brearley developed what is widely regarded the first “rustless” – now known as stainless steel – in 1913. The contract between Marcegaglia and Primetals Technologies was signed in the Harry Brearley suite, a part of Marcegaglia’s on-site conference center, as a tribute to the rich history of Sheffield.
Marcegaglia’s Sheffield site, a U.K. leader in green steel production compared to blast furnace-based producers, will see further efficiency and environmental improvements through this EAF upgrade project. Primetals Technologies’ modernization of the EAF plant will further enhance the plant’s efficiency and ecological compatibility. To ensure a short down time, larger furnace components will be preassembled, and completion is scheduled for mid-2026. With this new EAF, Marcegaglia aims to increase plant productivity to over 500,000 tons per year of stainless steel products, which will be further processed within Marcegaglia Group.
An Optimized Melting Process
The project involves completely rebuilding the existing furnace with a larger diameter and volume to facilitate scrap charging and reduce delays. In this way, the melting process will be optimized. The new 7.1-meter furnace diameter will maximize the use of the existing transformer power and allow for shell exchange practices designed to minimize downtime. Additionally, furnace operations will be sped up thanks to an upgraded hydraulic unit and a redesigned furnace platform.
As a result of the extensive revamp the production process will be enhanced by the installation of a dedicated burner system and a lime-dolo injection system. The dedusting system will be upgraded with new water-cooled ducts and a drop-out box, ensuring precise furnace pressure control and improved extraction of increased thermal power from fumes.
Leading Provider in Stainless Steel Production
Dr. Antonio Marcegaglia, President and CEO, and Dr. Emma Marcegaglia, Vice President and CEO, expressed their satisfaction in selecting Primetals Technologies as a partner for this investment. Several factors influenced the choice of supplier, including a solid reference base and the company’s leading expertise in stainless steel production. This project is not only economically and technically significant but also marks the Group's first venture into steel production.
Marcegaglia Group, headquartered in Gazoldo degli Ippoliti, Italy, is a world leader in steel product transformation. With a total production capacity of 6.5 million tons of carbon and special steels, the Group employs some 7,500 people and operates 36 plants spread across four continents.
- HyREX – a new process technology for low-carbon hot metal production
- Hydrogen-based direct reduction process
- Direct use of sinter feed
- Electric smelter furnace (ESF) used to melt DRI fines
On July 22, 2024, Primetals Technologies and POSCO signed a cooperation agreement to design and implement a HyREX demonstration plant. Based on a memorandum of understanding (MoU) signed in 2022, POSCO and Primetals Technologies are now realizing the plant at POSCO’s premises in Pohang, South Korea. A core aim of the plant is to test and verify certain details of the production process while determining the most cost-effective process parameters.
The global iron and steel industry is targeting a reduction of carbon dioxide emissions, and hydrogen-based direct reduction technologies based on the HyREX process will allow steel producers to replace carbon-intensive blast furnaces.
HyREX Process Overview
HyREX is a new process that combines the FINEX direct reduction process with an electric smelting furnace (ESF) to produce liquid hot metal. POSCO and Primetals Technologies started developing FINEX in 1992. The FINEX process charges iron ore and uses a cascade of fluidized-bed reactors to produce direct-reduced iron (DRI). While the FINEX process utilized reduction gas from coal gasification, HyREX uses hydrogen as reduction gas. In combination with an ESF, hot direct-reduced iron is transferred for the final reduction process, melting, carburization, and slag formation, to produce liquid hot metal of similar quality to that stemming from blast furnaces, but with significantly reduced carbon emissions.
HyREX Plant Overview
The HyREX industrial demonstration plant will consist of an ore dryer, fluidized-bed reactors arranged in a cascade, a hot DRI transport system, the ESF, a dedusting system, metal tapping, and slag granulation as key equipment. Seeking to replace blast furnace based ironmaking, HyREX can be fed with sinter feed, removing the environmentally intensive sintering process and the need for a coke plant. HyREX technology is suitable for more than 50 percent of globally available iron ore grades.
- Meets greater local market demand for high-quality stainless steel products
- Yantai Walsin achieves tighter tolerances and improved surface quality
- Lower production costs with in-line processing
Primetals Technologies has received the final acceptance certificate (FAC) from Yantai Walsin Stainless Steel for a new stainless steel combination mill , enabling Yantai Walsin to produce 420,000 tons per year of stainless steel and nickel alloy products. This new mill meets the increase in market demand for high-quality stainless steel products in China. For Yantai Walsin, this trend suggests that it converts billets from its existing plant into finished products that achieve tighter tolerances and improved surface quality, which reduces the amount of peeling after pickling and therefore saves costs.
A further benefit for Yantai Walsin was the fact that the bar-in-coil outlet realizes in-line quenching for austenitic and ferritic stainless products, leading to a reduction of subsequent post-processing annealing. Moreover, Primetals Technologies has designed the equipment to accommodate a future addition of an in-line solution for the direct treatment of wire rod products, which also reduces subsequent post-processing annealing. For bar products, the producer now uses a rapid transfer system to slow cooling bins for martensitic grades.
A Complete Solution
Located in Yantai, Shandong Province, China, the new mill project was completed via a consortium consisting of Primetals Technologies and CERI Long Products. The scope comprised all electrics and automation to approach Industry 4.0. The combination bar and rod mill includes three outlets: a straight bar outlet for the production of bar from 40 millimeters to 130 millimeters, a bar-in-coil outlet to produce bar from 18 millimeters to 40 millimeters in coils and a wire rod outlet to produce rods from 5.5 millimeters to 18 millimeters in coils.
The mill train features a next-generation breakdown mill, induction heating system, roughing and intermediate mill with no-housing stands which feed a cooling bed equipped with abrasive saws, slow bin cooling, bundle-forming stations and in-line bar straightening. The bar-in-coil outlet will utilize the latest high-speed pouring reels with direct quenching. The rod outlet includes a Morgan No-Twist Mill, Morgan Rod Reducing/Sizing Mill, Morgan Stelmor Conveyor, vertical pallet coil handling, as well as a high-speed shear system and a future in-line direct solution treatment line.
State-of-the-Art Quality Control
Primetals Technologies’ electrical and automation supply includes electrical equipment, a Level 1 and Level 2 process automation system (the Long Rolling Process Expert) and mechatronics packages. Developed by Primetals Technologies, The Long Rolling Process Expert is a production management platform that includes Quality Expert, which provides Through-Process Quality Control functions.
In a letter highlighting Primetals Technologies as the consortium leader of this project, Yantai Walsin Vice President of Engineering, Wen-Nan Hung, said, “Throughout the duration of the project, Primetals Technologies took full responsibility for several critical aspects, including process design, process layout, and overall project execution.”
“We have recognized Primetals Technologies to be a reliable and highly competent partner. Their contributions were instrumental in the successful completion of the project.”
Walsin Lihwa Corporation, established in 1966, is an industrial conglomerate with operations spanning wire and cable, stainless steel, and renewable energy.
No-Twist and Stelmor are registered trademarks of Primetals Technologies in certain countries.
Photo: Curved section of Primetals Technologies’ Stelmor Conveyor for future in-line direct solution treatment (DST) processing.
- Primetals Technologies to design and supply the world’s most advanced pellet pot testing facility
- Allows for fast and reliable pot grate test results
- Future implementation of direct reduction and electric steelmaking plants at Tata Steel Nederland’s site in IJmuiden emphasizes need for well-structured and carefully developed pellet-feed mixtures
Tata Steel Nederland has chosen Primetals Technologies’ pellet pot testing facility solution for its pilot plant located in IJmuiden, the Netherlands. Primetals Technologies will design, supply, and implement the equipment for Tata Steel Nederland’ s research and development department (Tata Steel R&D Technologies) along with a comprehensive electrical and automation solution. Startup of the new facility is scheduled for mid-2025.
Primetals Technologies has been operating an innovative pellet pot in Leoben, Austria, since 2014. With Tata Steel Nederland’s pellet pot testing facility, Primetals Technologies will take this concept to the next level in terms of capacity, level of autonomous operation, and special features – the latter are designed to replicate the configuration of Tata Steel Nederland’s industrial pelletizing plant.
"This is one of Tata Steel R&D’s largest investments in years," said Vincent Ritman, director of Tata Steel R&D. "In working with Primetals Technologies, we are bringing in a reliable and knowledgeable partner who will help us to make the connection between the pellet plant and the future direct reduction plant possible. The installation can produce high-quality and uniform pellets on a large scale, 65 kilograms, for the current pellet research program.”
The Next Level of Pellet Testing
Thanks to Primetals Technologies’ own testing facility in Austria, the pellet pot concept is a tried-and-tested system. It enables fast and comprehensive testing of various concentrates and pellet-feed mixtures as well as detailed analysis and determination of optimal temperature profiles tailored to Tata Steel Nederland’s pellet quality targets.
Primetals Technologies will design Tata Steel Nederland’s pellet pot to handle up to six pot grate tests per day and 500 tests annually. The pellet testing facility also features a system for off-gas analysis, which will generate valuable insights on emission levels.
Carbon Neutrality by 2045
Tata Steel Nederland has the ambition to reduce CO2 emissions by 40 percent by 2030 and to become carbon neutral by 2045. At its IJmuiden site, this is a process encompassing the whole ironmaking and steelmaking value chain. In terms of equipment, the transition will result in a switchover to gas and hydrogen based direct-reduced iron technology along with an electric arc furnace based steelmaking plant.
The implementation of the new ironmaking and steelmaking plants means that Tata Steel Nederland will operate partly with new types of raw materials, while dealing with higher requirements on pellet qualities. As a result, the new state-of-the-art pellet testing facility will play a key role both in ensuring optimal raw material mixes for the pelletizing plant and in optimizing the parameters for the induration process.
Premium Steel Products
Tata Steel Nederland is one of Europe’s largest steel producers and supplies high-grade steel products to demanding sectors all over the world, including the construction, automotive, and packaging industries, as well as producers of industrial machines. The research and development department, Tata Steel R&D Technologies, is an important part of the company. In close cooperation with customers, the department designs new steel products that will help them stand out from their competition.
Tata Steel Nederland comprises two business units, Tata Steel IJmuiden and Tata Steel Downstream Europe, and is part of Indian global steel company Tata Steel.
Tata Steel Nederland has tasked Primetals Technologies with the implementation of an advanced pellet pot grate testing facility. From left to right: Piotr Ksen, Project Manager, Hans-Jörg Baumgartner, Process Engineer, both with Primetals Technologies; Jan Baalbergen, Project Manager at Tata Steel IJmuiden; Christoph Aichinger, Head of Agglomeration, and Thomas Marton, Commercial VP Ironmaking, both with Primetals Technologies.
- Primetals Technologies celebrating 100 installations of electrode control system Melt Expert
- Key success factors are a high level of precision and effective optimization of electric arc furnace melting processes
- Major benefits for steel producers include productivity gains and cost-savings stemming from lower consumption figures
Athletes who excel at the 2024 Summer Olympics in Paris all have certain characteristics in common – they are precise and effective, and they showcase world-leading skills in their respective discipline. Interestingly, all of these features can also be found in Primetals Technologies’ Melt Expert electrode control system for electric arc furnaces (EAFs) and ladle furnaces (LFs).
Melt Expert customers worldwide benefit from increased productivity, reduced energy and electrode consumption, as well as lower production costs. Simply put, the leading system for optimizing melting processes is a game-changer for steel producers wanting to get the most out of their EAFs and LFs. Recently, Primetals Technologies celebrated its 100th Melt Expert installation at a customer’s site in Turkey. All of these implementations were accomplished within the last four years.
100 Melt Expert Installations
The recent Melt Expert installation at an EAF in Turkey is a significant milestone. Melt Expert enables dynamic control over the melting process, increases process stability, and helps the meltshop staff to overcome scrap fluctuations. The integrated Foaming Slag Manager and the Dynamic Spray Cooling model ensure additional process control and efficiency improvements. The comprehensive diagnostics package provides operators with detailed melt diagnostics, electrode consumption figures, and key performance indicators via an intuitive dashboard.
Precision and Control in Melting Processes
Automation experts from Primetals Technologies have spent years of hard work to perfecting Melt Expert’s performance, making it the true champion in the field of electrode control systems for EAFs and LFs. Melt Expert offers numerous benefits to process engineers, plant managers, and maintenance personnel – it significantly increases furnace productivity by addressing the common problem of reduced throughput and efficiency in steelmaking processes. It also tackles the high energy costs associated with the melting process by lowering the consumption of electrical energy. The system ensures the accurate reproduction of a predefined melting process, solving the problem of operational inconsistency and lack of precision. Moreover, it optimizes the melting process by improving overall furnace performance and output quality.
Ensuring Peak Performance
Just like sports equipment, Melt Expert must stay in shape to continuously unfold its full potential. Primetals Technologies offers worldwide service support, including on-site assistance, to keep the system and its settings optimally adjusted to changes in factors such as scrap density and quality. Service contracts provide troubleshooting support, system maintenance checks, optimization based on data analysis, and a guaranteed response time.
By signing an annual service contract, steel producers benefit from several advantages. A dedicated, expertly staffed support hotline helps to resolve any production-related issue swiftly and comprehensively. Remote live support gives specialists from Primetals Technologies immediate access to critical data for analysis and insight that may not be known to the customer.
The Melt Expert electrode control system has been installed 100 times at electric arc and ladle furnaces.
- Primetals Technologies, Shagang Group, and Castrip have installed three Castrip lines to produce thin-gauge sheet
- Reduced energy consumption and lower CO2 emission levels for ultra-thin strip production
- Shagang to produce value-added steel grades, meeting the requirements of a wide range of applications normally consisting of cold-rolled sheet
- Castrip suitable for steel producers operating either EAFs or LD converters (BOF)
Ultra-compact and energy-effective Castrip plants were first installed in the U.S.A. and Mexico. In 2018, Shagang Group introduced Castrip technology to China at its plant in Zhangjiagang, Jiangsu Province. Since then, Shagang Group has invested in three further Castrip lines. These new lines were implemented in just 12 months, with the latest becoming operational in June 2024. Shagang Group has already granted the final acceptance certificate (FAC) to Primetals Technologies for the first two lines. In total, Shagang now operates four Castrip lines.
The startup of lines No. 2 and 3 was exceptional in terms of duration and efficiency, thanks to the close and effective collaboration between the project partners, including Primetals Technologies, Shagang Group, and Castrip. Primetals Technologies was responsible for the engineering and supply of core mechanical equipment, technological packages, and automation systems. The entire line is controlled by fully integrated basic (Level 1) and process optimization (Level 2) automation systems, which control all casting and rolling operations.
Lowest Emission Levels in the Entire Industry
Castrip plants are defined by highly flexible ultrathin cast strip (UCS) production at the industry’s lowest energy consumption and emissions levels. Two main factors allow for this remarkable achievement – first, there is no need to reheat the strip, and second, Castrip lines produce strip of close to net shape, which lowers the amount of rolling force needed to meet product requirements. Castrip is therefore an attractive alternative for steel producers looking to decarbonize the production process.
An Uninterrupted Process
During the Castrip casting process, liquid steel from the meltshop passes through two counter-rotating rolls producing a continuously cast steel strip. The ultra-thin cast strip (UCS) product leaving the caster roll nip then enters an area of the plant with a controlled atmosphere, called the “Hot Box”. This sealed environment reduces the levels of oxidation and prevents excessive scale formation on the newly formed strip. Thanks to the “Hot Box” process, there is no need to descale the strip.
A Castrip line also consists of a single stand hot-strip mill, which reduces strip thickness by 10 to 55 percent. The hot-rolled strip then enters a cooling zone where a controlled decrease in temperature takes place, allowing the strip to meet the desired physical properties. In the next step, the strip is guided towards one of the two coilers, and a rotary drum shear is used to separate the strip, resulting in an uninterrupted process starting from the upstream area and continuing all the way through the Castrip plant.
Increased Hot-Strip Mill Output
Castrip is the ideal solution for steel producers entering the flat steel market, as well as for those looking for additions to their long product portfolio. Castrip also works especially well for creating and producing special steel grades of various types – producers investing in a Castrip line can relieve their hot-strip mill of demanding thin gauges and, in that way, increase the output of the hot mill.
Castrip steel sheet is used, for example, in the construction, purlins, steel framing, steel decking, and racking/storage industries, as well as in lightweighting items for the agriculture sector, automotive parts, and the welded tube industry. Ultra-thin cast strip (UCS) and hot-rolled coils are used as a direct replacement for cold-rolled products and can also be cold-rolled as thin as 0.25 millimeters to expand product ranges.
Primetals Technologies is a licensee of Castrip and provides equipment and automation for Castrip installations.
The Shagang, Castrip, and Primetals Technologies teams commemorating the first coil produced on Castrip line No. 2.
Key facts: Shagang Group’s Castrip plants
Capacity
500,000 tons per year (per plant)
Line length
50 meters (from turret to coiler)
Caster roll diameter
500 millimeters
Dimension of cast strip
0.7 to 1.9 millimeters thick x 1,345 to 1,680 millimeters wide
Steel grades
LC, MC, HSLA, weathering grades, HC (≤0.65 C), high-strength (<1500 MPa)
- Primetals Technologies has implemented gas cleaning plant to increase dry dust recycling while reducing energy consumption and improving green credentials
- Lowers ongoing maintenance requirements
As part of ArcelorMittal’s initiative “Smarter Steels for People and Planet”, ArcelorMittal is focused on minimizing the environmental impact of their operations. This means investing in innovative iron and steelmaking processes that are more efficient, use less energy, and emit significantly less CO2. To support this purpose, ArcelorMittal Poland placed an order in 2021 with Primetals Technologies to supply a gas cleaning plant for its blast furnace No. 2 in Dąbrowa Górnicza, Silesia Voivodeship, Poland. Recently, ArcelorMittal granted the final acceptance certificate (FAC) to Primetals Technologies.
The gas cleaning plant is an essential component in any blast furnace complex and is responsible for ensuring emissions from the blast furnace are in line with environmental norms.
Advanced Technology
The new gas cleaning plant includes the complete system from the furnace offtakes through to the existing gas network. Primetals Technologies supplied the key components, including the cyclone, wet scrubber and demisting vessel. This has allowed ArcelorMittal Dąbrowa Górnicza (AM DG) to increase the amount of dry dust recovered for recycling and reduced the requirement for waste-water processing. Additional benefits from the new equipment are an improvement in energy efficiency of the plant and downstream units and a reduced need for maintenance-related labour. This has made the whole plant more cost-effective to run and improved the green credentials of the operations.
Project Excellence
Construction of the new gas cleaning plant was undertaken by consortium partner Mostostal Zabrze Realizacje Przemyslowe (MZRP). With a 90-day shutdown window for demolition and construction, the major units were built in parallel to blast furnace operation, thereby minimizing the work required during the shutdown period. These modular units were then lifted into place utilizing a 1000-ton crane.
A World Leader
ArcelorMittal is the world's leading steel and mining company, and the dominant steel producer in Poland, operating six production plants in the south of the country. Its range of products includes profiles, rails, fittings for the construction, transport, and mining industries, as well as flat products for the automotive industry and the manufacture of domestic appliances. The Dąbrowa Górnicza plant specializes in producing heavy profiles. It is also one of a few plants worldwide able to produce 120-meter-long rails.
ArcelorMittal Dąbrowa Górnicza blast furnace No. 2 with new gas cleaning plant from Primetals Technologies.
- Primetals Technologies will upgrade existing vacuum degasser (VD) plants to vacuum oxygen decarburization (VOD) systems, enabling Acciaieria Arvedi to produce electrical steel
- Italian steel producer has ambitious plans to expand its portfolio and enter new markets
Leading Italian steel producer Acciaieria Arvedi has recently tasked Primetals Technologies with an upgrade of its two vacuum degassers (VD) at the steel plant in Cremona, Italy. The project is scheduled to be completed in the second half of 2025.
For the near future, Arvedi has ambitious plans to expand its product portfolio to encompass both electrical and ULC/IF steel grades. Traditionally, these types of steel grades are manufactured through the LD converter (BOF) – ladle furnace (LF) – RH-degasser route. Arvedi plans to pioneer the production of electrical steels with the electric arc furnace (EAF) – LF – VD-OB route, as one of the world’s first steel producers to choose this approach.
Enhanced Vacuum Degassing Process
Arvedi will upgrade its VD plants to vacuum oxygen decarburization (VOD) systems capable of handling the vacuum degassing and oxygen blowing process under vacuum conditions for the manufacture of silicon steel. Primetals Technologies will supply key mechanical components, including water-cooled copper-plated ladle covers, oxygen lance systems, gas coolers, vacuum control systems, and waste-gas burners. Experts from Primetals Technologies will also support Arvedi in the development and fine-tuning of the vacuum degassing process steps from the get-go.
Designed to Avoid Skull Formation
The VOD plants, which are tank degassing units equipped with oxygen blowing lances, are designed for handling extra-low-carbon steel grades together with the addition of aluminum and/or silicon during the process. Arvedi’s new equipment will feature copper-cladded, water-cooled ladle covers from Primetals Technologies, designed to avoid skull formation. These kind of ladle covers will also reduce the need for maintenance-related work and, in addition, enhance occupational safety at the plant.
Europe’s First Mini-Mill for Flat Products
Acciaieria Arvedi’s Cremona plant, in operation since 1992, is Europe’s first and the world’s second mini-mill for the manufacture of flat-rolled steel. Current plant capacity is at four million tons per year through a process route consisting of EAF, LF, VD, ESP/ISP plants. The Arvedi group is Italy’s largest steel producer and is currently active in carbon steel production, which includes top-notch HSLA grades for the automotive industry, and serves the market for stainless steel. The business is mainly focused on European industrial sectors.
Primetals Technologies will upgrade Acciaieria Arvedi’s VD plant, enabling the Italian steel producer to produce electrical steel.
- Primetals Technologies to supply 2-strand continuous slab caster with optimized roll geometry
- Will be designed for both conventional and silicon steel production
- Third large casting project in three months demonstrates the close and decades-long collaboration between Baosteel and Primetals Technologies
The world’s largest steel producer, Baosteel, a part of Baowu Group, already operates more than 20 casters supplied by Primetals Technologies. The close collaboration, based on mutual trust, was established in the 1990s. On June 18, 2024, Baosteel signed a contract with Primetals Technologies for the latest continuous casting project, this time for a plant in China’s Shanghai region. It is the third caster order from Baowu Group in three months, a fact that further underscores the strong partnership between the two companies.
The new continuous caster No. 6 will produce both conventional and silicon steel grades for various industries including home appliances and automotive. Primetals Technologies will supply the mechanical equipment and a comprehensive scope of Level 1 and 2 automation systems, and will provide construction and implementation services.
Next-Level Continuous Caster Design
A well-balanced combination of sophisticated mechanical design and future-proof automation and digitalization solutions is essential for producing demanding steel grades. Baosteel’s new caster will feature several innovative technologies – this in combination with Primetals Technologies’ established continuous casting expertise and innovation leadership, underscored by a large number of patents, were some of the key factors behind Baosteel’s choice of supplier.
Highly Innovative Solutions
Experts from Primetals Technologies will establish the ideal caster roll geometry already at the design stage. This is thanks to a ground-breaking model recently developed by Primetals Technologies, which reduces mold level fluctuations stemming from unsteady bulging by 50 percent, leading to both higher casting speeds and greater productivity.
A comprehensive suite of automation and technology solutions ensures that Baosteel’s new caster will produce slabs with top-level inner quality – an important feature for the manufacture of demanding silicon grades. The Smart Mold, a high-performance cassette-type mold, will be configured with the DynaWidth online mold-width-adjustment system for flexible and fast slab-width changes. Together, these systems make sure that high-quality conditions are met early in the casting process. An electromagnetic stirrer is a key part of the mechatronics package and allows for enhanced inner-strand quality.
DynaPhase, Dynacs 3D, and DynaGap Soft Reduction 3D are dynamic secondary cooling and soft-reduction packages, which drastically contribute to quality improvements by calculating thermodynamic effects such as conductivity, density, and strand temperature.
Continuous Improvement of Product Quality
Several expert systems round off the extensive scope of automation and technology solutions. The computer-aided quality control system Quality Expert tracks, controls, and supervises quality-related data. This technology also makes quality prediction for the cast products, contributing to continuous improvement of product quality. The Nozzle Expert checks the condition of the secondary cooling system online and detects clogged nozzles and leakages with high accuracy.
A Wide Range of Flat and Wide Products
Baosteel is a part of the China Baowu Steel Group Corporation, a Fortune Global 500 enterprise. The company operates several plants, including locations in Shanghai, Wuhan, Meishan, and Zhanjiang. Baosteel’s product portfolio encompasses a wide range of flat and long products based on carbon, low-alloyed, alloyed, and silicon steel grades for use in various applications.
Primetals Technologies will supply Baosteel with a 2-strand continuous caster designed for both conventional and silicon steel production.
Key facts: Baosteel’s 2-strand continuous caster
Capacity
2.35 million tons per year
Radius
9.5 meters
Metallurgical length
37 meters
Dimension of slabs
230 x 900 to 1,450 millimeters
Steel grades
silicon (NGO, GO), automotive, ultra-low-carbon, low- and medium-carbon, peritectic
- New internal combustion chamber type stove will be added to blast furnace No. 5 “Kalyani”
- Project includes extension of hot blast main to accommodate the additional stove
- Additional hot blast stove ensures the security of operations and enables existing stoves to be taken offline for repair without affecting site operations
Primetals Technologies recently received an order from Steel Authority of India Limited (SAIL) for the design, supply, and installation of a new hot-blast stove for blast furnace No. 5, named “Kalyani,” of the IISCO steel plant at Burnpur, Asansol city, West Bengal, India. The addition of this fourth stove will enable IISCO to repair existing stoves without impacting plant production or efficiency. Implementation is scheduled to take place 17 months from the date of contact signing. Upon completion, the IISCO steel plant will benefit from the operational advantages of utilizing four stoves.
Efficient Combustion
The upcoming internal-combustion-technology stove includes a range of innovative features – including a “mushroom dome” developed for longer equipment lifetime due to its stable refractory design and a vertical ceramic burner to enable good mixing and efficient combustion. In addition, the hot-blast mains will be extended to accommodate the fourth stove.
Primetals Technologies will provide the design, engineering, manufacturing, and construction of the new stove shell. The supply also includes high-grade refractories, expansion joints, hydraulic systems and valves along with the hot-blast main extension and associated support and access structures.
Leading Integrated Steel Manufacturer
Steel Authority of India Limited (SAIL) is one of the largest steelmaking companies in India. SAIL produces iron and steel at five integrated plants and three special steel plants, located principally in the eastern and central regions of India and situated close to domestic raw material sources.
IISCO Steel Plant (ISP), a unit of SAIL, is one of India’s oldest integrated steel plants. Established as an industrial enterprise in 1918, the plant has been progressively modernized and expanded to a capacity of 2.5 million tons per year. It is now entering another period of expansion to enhance capacity by around four million tons per year. With three rolling mills at the site, SAIL IISCO manufactures a range of wire rod, bar, and section products.
Internal combustion stoves from Primetals Technologies installed in India.
- Primetals Technologies’ first-ever EAF Quantum started up 10 years ago at TYASA in Mexico
- Energy-efficient and reliable operation has resulted in an impressive 77,000 heats to date
- 15 EAF Quantum furnaces in operation worldwide, with more currently being constructed
Mexican steel producer Talleres y Aceros S.A. de C.V. (TYASA) and Primetals Technologies have recently reached a milestone for the world’s first EAF Quantum plant in Ixtaczoquitlan, Mexico. On May 7, 2024, the 100-ton electric arc furnace had been in operation for 10 years, boasting some 77,000 heats and a total production of almost eight million tons.
“We are happy to celebrate this milestone achievement together with Primetals Technologies,” says Oscar Junior Chahin, Co-CEO of TYASA. “Back in 2014, our clear target with the meltshop investment was to significantly increase our annual production while keeping operational costs down by utilizing the low power consumption levels of the EAF Quantum. 10 years later, we are pleased to say that the targets have been met, and the EAF Quantum has exceeded our expectations in terms of reliability and efficiency.”
Lower Operating Costs
Several technological innovations enable the EAF Quantum to reach remarkable performance figures. The scrap preheating system shortens the power-on times compared to conventional electric arc furnaces, where the scrap is charged cold. The EAF Quantum’s scrap-preheating technology utilizes off-gas from the production process. Less energy is therefore needed to melt the scrap, resulting in lower operating costs as well as reduced CO2 emissions.
The EAF Quantum can achieve power consumption figures below 300 kilowatthours per ton – with a power-on time of less than 29 minutes and a tap-to-tap time of less than 33 minutes.
Remarkable Tap-to-tap Time
There are 15 EAF Quantums in operation across the world to date, and several furnaces are currently being constructed and implemented. Several of these plants have recently attracted attention within the industry as they are showcasing remarkable performance figures. As an example, the EAF Quantum implemented at Chinese steel producer Guilin Pinggang has achieved tap-to-tap times of 31 minutes at power-off times of 4 minutes.
A Complete Minimill
Founded in 1985, TYASA is a privately owned company with two sites, the production location in Ixtaczoquitlan and a service centre in Mérida, the capital city of the Mexican State of Yucatán. With some 2,400 employees, TYASA produces special steel grades, flat steel, coated steel, and items for the construction sector.
Primetals Technologies has supplied TYASA with a complete minimill – the EAF Quantum, a twin ladle furnace, a twin vacuum degasser, and a continuous casting machine – as well as a reversing cold mill. TYASA has also ordered a CASTRIP production line, which is licensed by Nucor. To process strip from the CASTRIP line, the Mexican steel producer awarded Primetals Technologies with a contract to implement a combined galvanizing and color coating line in 2018.
TYASA’s EAF Quantum from Primetals Technologies has produced 77,000 heats since 2014. The EAF Quantum is characterized by lower operating costs and reduced CO2 emissions.
The EAF Quantum is designed to charge scrap via the innovative shaft into the operating furnace at the optimal time slot during operation. This is resulting in ongoing operation with ideal flat-bath conditions.
- Production capacity ramped up to maximum right from the start
- Tight deadline met despite challenges related to the Covid-19 pandemic
- Kobe Steel benefits from increased mill performance and competitiveness of its plates as well as a more stable product supply system
Primetals Technologies has recently received the final acceptance certificate (FAC) for a plate finishing mill at Kobe Steel’s plant in Kakogawa, Japan. This rolling mill was ordered in 2021 as Kobe Steel wanted to implement state-of-the-art equipment to improve product quality and further enhance its already short and stable delivery times. Primetals Technologies was responsible for the supply of core mechanical equipment, auxiliary and ancillary technologies, as well as on-site supervision for construction work and implementation.
Leading Supplier of Plate Mills
The plate finishing mill at Kobe Steel's Kakogawa Works had been in operation since 1972, i.e. for over 50 years. Kobe Steel choose Primetals Technologies as the supplier of the new mill mainly based on its extensive reference base regarding similar projects in Japan as well as other parts of the world.
Primetals Technologies managed to deliver and implement the mill on schedule although the project started while supply chains and many other processes still were heavily affected by restrictions and constrains related to the Covid-19 pandemic. The timely implementation was made possible mainly thanks to close collaboration and efficient communication between the Primetals Technologies team and personnel from Kobe Steel.
Enhanced Performance
Featuring the most modern solutions, the new finishing mill showcases Primetals Technologies’ determination to carefully design advanced rolling mill technology. It processes plates with thicknesses from 4.5 to 360 millimeters at widths of 1,000 to 4,500 millimeters. The plate finishing mill enables Kobe Steel to enhance mill performance both in terms of product quality and delivery times while increasing its competitiveness within the steel plate industry.
Highly Durable Steel Plates
Kobe Steel is a global company that operates worldwide under the unified group brand “KOBELCO”. The company's proprietary portfolio of steel plate products includes Ecoview Plus, a highly durable steel plate for the bridge sector, and EX-Facter, a fatigue-resistant steel plate with longer lifetime than conventional steel plates.
Primetals Technologies has recently received the FAC for a new plate finishing mill implemented at Kobe Steel’s Kakogawa Works. Copyright: Kobe Steel
- 12-meter long MULPIC line was supplied to replace existing laminar cooling system at a plate Steckel mill in India to achieve higher cooling rates
- Enables mill to increase product quality and expand pipe-grade product portfolio
Recently, Primetals Technologies signed the final acceptance certificate (FAC) with a steel producer in India following the successful installation and commissioning of a new Multi-Purpose Interrupted Cooling (MULPIC) system for a plate Steckel mill line. The technology offers an ‘in-line’ plate cooling system capable of reaching the desired cooling rate and temperature drops necessary for plates of various product dimensions.
This advancement has expanded the mill's product range to include higher grades used for pipeline applications, making them suitable for the most demanding markets, such as the oil and gas industry.
Improvements in Product Quality
The MULPIC technology is an in-line and integrated plate cooling system that is offered as a complete mechatronics package, combining the mechanical equipment with smart process control technology. The system comprises high precision valves with large flow range. It also features high water nozzle density and actuators with advanced flow control valves as well as crown and edge masking control functions. The MULPIC technology has the capability for both accelerated cooling and direct quench cooling across a wide range of product thicknesses. This ensures superior cooling performance and maintains uniform, controlled temperatures along the length and width of the plate, resulting in improved flatness and uniform mechanical properties. This, in turn, is leading to improved product quality.
Expanded Product Offering
The upgrade of the existing laminar cooling system with MULPIC technology enabled the plate Steckel mill to achieve higher flow density and cooling rates. This cooling upgrade allowed the plate mill to process higher-strength steel grades such as X70, accommodating plate thicknesses between 10 and 30 millimeters and widths of up to 4,500 millimeters with excellent temperature and flatness uniformity.
This advanced cooling methodology rapidly removed heat, providing metallurgists with increased flexibility when designing new alloys for entering new markets. Additionally, it reduces operating costs through lean alloying.
The Online Plate Cooling Technology: MULPIC
Primetals Technologies designed and supplied the entire in-line plate cooling system comprising two cooling banks with each bank measuring six meters in length. Each bank consists of six top and six bottom headers, and the height of each header can be adjusted between 500 and 1200 millimeters to ensure ultra-precise cooling of every single plate. The top and bottom headers are made of stainless steel to prevent corrosion, guaranteeing a long lifetime. The MULPIC system was also designed to optimize the mill’s overall carbon emissions.
MULPIC - world-leading plate cooling technology from Primetals Technologies.
- Central Operation Cockpit (COC) enables single-operator control of multiple plant sections
- Reduces need for manual intervention in the production process, which results in increased productivity, more stable production, and reproducible and high end-product quality
- First reference of COC to be implemented at thyssenkrupp Steel’s Duisburg plant
Primetals Technologies has developed a highly innovative operational system, the Central Operation Cockpit (COC) , that allows for controlling a whole plant from one single point. The operator is supported by numerous intelligent and AI-backed assistants to get a full-fledged bird’s-eye view of the entire production process.
thyssenkrupp Steel has recently taken an important step toward an autonomous plant, by tasking Primetals Technologies with the implementation of a COC concept at its hot-strip mill No. 1 in Duisburg. During the first project phase, which lasted until the end of March 2024, thyssenkrupp Steel and Primetals Technologies designed an operational concept for the COC system, tailored to thyssenkrupp Steel’s current and future needs. The project has now entered Phase 2, the implementation of the system, and this phase is scheduled to be completed by the beginning of 2025.
Controlling Multiple Plant Sections
Steel producers currently look at solutions for reducing production-related manual interventions to become more productive and increase product quality. At the same time, an increased number of automation systems may result in a more demanding and complex monitoring process. To address and overcome this problem, Primetals Technologies has developed the COC.
With this new concept, a single operator can control multiple plant sections via a highly intuitive interface. A large display wall provides all the necessary information and can instantly switch between any of the numerous cameras deployed at the mill. This is especially helpful if any of the numerous assistant systems detects a potential issue that requires urgent attention, or if user-defined events take place. The COC is equipped with an intuitive configuration tool, and it is easy and convenient for steel producers to extend and modify the cockpit according to any changing needs. As a result, there is no risk of information overflow.
Highly Customizable Display Wall
The intuitive and operator-friendly interface is backed by the intelligent video management system SynX Supervision developed by Mitsubishi Heavy Industries in close collaboration with Primetals Technologies. The display wall is highly customizable: the operator can, for example, dedicate screens to specific assistant systems or areas of the plant.
The COC unites a wide variety of digital assistant systems. Together, they ensure that the operators have all the information they need to operate the plant efficiently. As an example, the Ski Assistant – developed by Primetals Technologies – is designed to alert operators of skis that emerge during production. Seamless integration into the COC enables the operator to act swiftly on insights delivered by the assistant systems.
Climate-Neutral Steel by 2045
thyssenkrupp Steel employs 26,000 people and has a production capacity of about 11 million tons of crude steel annually. The leading German steel producer has set itself a goal to reduce CO2 emissions by more than 30 percent by 2030, and to produce climate-neutral steel by 2045. The strategy includes Scope 1 and 2 emissions, which means not just direct but also indirect emissions from purchased energy.
The Central Operation Cockpit (COC) from Primetals Technologies is a ground-breaking concept that enables one single operator to run a whole plant.
- Primetals Technologies to supply bow-type 2-strand continuous caster with a reduction force of 5,000 kilonewton per roll
- Will produce slabs of thicknesses of up to 450 millimeters at widths up to a remarkable 2,700 millimeters
- Annual capacity at 3.5 million tons for the production of high-quality, ultra-thick plates
Chinese steel producer Baosteel Zhanjiang has awarded Primetals Technologies a contract for the engineering, supply, and startup of a bow-type 2-strand continuous caster for the production of extraordinarily thick slabs. The caster, designed to be one of the world’s most powerful, will be implemented at Baosteels’s plant in Zhanjiang, Guangdong province. It will produce slabs of record-breaking sections, measuring up to 2,700 millimeters in width at 450 millimeters in thickness.
Primetals Technologies is responsible for the engineering and implementation as well as the supply of mechanical equipment and a comprehensive Level 2 automation package. With an annual capacity of 3.5 million tons of high-quality slabs, the new equipment will enable Baosteel to produce plates for heavy-gauge sectors like the shipbuilding and wind turbine industries. Usually, ingot casters or vertical casters are the equipment of choice for products of these thicknesses. However, both of these are not as cost-effective and efficient as Primetals Technologies’ new type of bow-type continuous slab caster.
Consistent and High Quality
Baosteel’s caster will be equipped with unique Single Roll DynaGap (SRD) segments from Primetals Technologies. When changing parameters that influence production, like steel grade, cooling practice, and casting speed, the process models of the Level 2 automation package dynamically determine the best casting gap, allowing for the SRD segments to optimally adjust individual roll gaps and forces. The caster’s SRD segments can handle capacities of 5,000 kilonewtons per roll, enabling very large thickness reductions in the casting process. This leads to superior internal quality of the cast slabs, and, in turn, results in the production of defect-free ultra-thick plates of high quality.
Mold Level Fluctuations Cut in Half
Another key feature of the caster is Primetals Technologies’ new and ground-breaking method for establishing the ideal caster-roll geometry at the initial design stage. This optimized roll geometry reduces mold level fluctuations stemming from unsteady bulging by 50 percent, enables higher casting speeds, and leads to greater productivity. A wide spectrum of parameters, such as targeted steel grade, section size, and casting speed, is taken into account by the software tool when it calculates the optimized geometry. As a result, it identifies just the right frequency spectrum for the rolls.
Reduced Energy Consumption
Primetals Technologies will implement the proven DynaFlex oscillator concept featuring a special design concept – engineers at Primetals Technologies have found a way to compensate for heavy mold weights by utilizing helical springs. Among the benefits is significantly reduced energy consumption levels.
The continuous bending and straightening concept from Primetals Technologies, Smart Segments, together with a dry-casting machine design that includes Eco Star rolls contribute to significantly improved slab-surface quality. The Eco Star rolls’ internal cooling system is capable of enduring the high temperatures needed to minimize surface defects during the dry-casting process.
A part of the China Baowu Steel Group Corporation, which is a Fortune Global 500 enterprise, Baosteel represents an integrated iron and steel company that operates several plants, including locations in Shanghai, Wuhan, Meishan, and Zhanjiang, and others. Baosteel’s product portfolio encompasses a wide range of flat and long products based on carbon, low-alloyed, alloyed, and silicon steel grades for use in various applications.
Key facts: Baosteel’s 2-strand slab caster
Capacity
3.5 million tons annually
Radius
12 meters
Metallurgical length
44 meters
Dimension of slabs
300 to 450 millimeters (thickness) x 1,600 to 2,700 millimeters (width)
Steel grades
medium-carbon, high-carbon, peritectic, high-strength low-alloyed (HSLA), pipe
- Circular Pelletizing Technology (CPT) revolutionizes pelletizing – has established new standard in cost-efficiency
- First reference plant producing at full capacity in India
- Low cost, low footprint alternative to conventional pelletizing plants
Indian iron ore mining company Essel Mining and Industries Limited (EMIL) recently granted the final acceptance certificate (FAC) to Primetals Technologies for its Circular Pelletizing Technology (CPT) plant located at its facilities in Basantpur, Odisha state, India. CPT is the world’s most compact pelletizing plant for the production of high-quality pellets, featuring an indurating furnace with unique circular design.
The CPT plant – the first of its kind – was successfully put into operation in October 2020, in midst of the pandemic. Since then, there has been an ongoing ramp-up of the production capacity. “With the support of the Primetals Technologies team, we were able to optimize pellet production and have continuously improved both the production capacity and pellet quality. We are still exploiting the full potential of the CPT pelletizing system.” says Pavan Kumar Kakani, Joint President and Unit Head of the EMIL plant in Basantpur.
With a design capacity of 1 million tons per year, the CPT plant processes local iron ores to produce pellets for both the export and domestic market.
Reduced Space Requirements
A CPT plant ensures that space requirements for the induration furnace are reduced by 50 percent compared to conventional pelletizing plants. As a result, the weight of the equipment and the building structure are significantly lower. The pelletizing process required less energy, as the CPT process is designed to optimize the thermal efficiency of the recycled hot process gas. This leads to lower operational expenses (OPEX). Primetals Technologies’ scope of supply included the complete plant design, full basic (Level 1) and process (Level 2) automation systems, as well as advisory and startup services including construction works and supervision during implementation.
A Fortune 500 Member
Established in 1950, Essel Mining and Industries Limited (EMIL) is part of the Aditya Birla Group, a global conglomerate and Fortune 500 member. Aditya Birla Group is active in a wide range of sectors including metals, chemicals, textiles, cement, and renewable energy. One of India’s largest mining companies, EMIL is also a producer of noble ferro alloys.
- New bar-in-coil (BIC) outlet will enable Hebei Xinggang Technology to manufacture products of superior coil shape and surface quality
- Work started in August 2023 and is expected to be completed in late 2024
- Hebei Xinggang to produce 16 to 52 millimeter bar from 160 to 180 millimeter square billets at a line speed of 18 meters per second
Primetals Technologies is supplying a new bar-in-coil (BIC) outlet for the Hebei Xinggang Technology plant, which is being relocated to Xingtai City, Hebei Provence, China. For this custom production process and equipment solution, Primetals Technologies will engineer, install, and implement a new BIC outlet. Also included are two shears, a water cooling line with closed-loop temperature control system, two latest-generation pouring reel coiler machines, a product-surface-friendly guiding and coil handling system, a vertical stem pallet system, and a comprehensive mechatronics package.
A Holistic View
Hebei Xinggang Technology preferred the Primetals Technologies solution because it took the entire production chain into consideration instead of focusing only on equipment. Hebei Xinggang Technology also considered the performance reputation of the Primetals Technologies Enhanced Temperature Control System (ETCS), which it had previously chosen as part of a second wire rod mill ordered from Primetals Technologies. The company also factored in Primetals Technologies’ successful track record of delivering similar BIC projects for five customers in the Asian market.
Producing Bar with Less Waste
BIC is a relatively new process for producing special-steel straight bar in the form of rolled coils of high quality. It allows steelmakers and suppliers to store inventory more efficiently and produce different kinds of bar with less waste and labor.
“Our BIC solution is state-of-the-art in terms of speed, reliability, and process flexibility,” says Mengmeng Li, China Sales Operation Manager at Primetals Technologies. “Hebei Xinggang will use it to maintain its position as a leading quality steel supplier in one of the world’s most competitive markets.”
The project is on a fast track. Work began in August 2023 and is projected to be completed in late 2024, along with two wire rod mills, which Hebei Xinggang Technology has ordered from Primetals Technologies. For the BIC line, Primetals Technologies will provide engineering and services via its long rolling business based in Sutton, Massachusetts, the U.S.A. Primetals Technologies’ regional company in China will provide equipment and overall project management.
Once complete, the solution from Primetals Technologies will enable Hebei Xinggang Technology to manufacture a product of superior coil shape and surface quality. The BIC line will turn 160 to 180 millimeter square billets into bar measuring 16 to 52 millimeters in diameter at speeds of up to 18 meters per second. Finished coils will weigh up to 2.5 tons.
Primetals Technologies will provide a new bar-in-coil (BIC) outlet for Hebei Xinggang Technology. This project and the implementation of two wire rod mills from a prior order are expected to be completed in late 2024. Pictured in the photo are representatives from Hebei Xinggang and Primetals Technologies.
- Primetals Technologies to supply and implement comprehensive upgrade of Level 2 automation system
- State-of-the-art process models will increase accuracy and reliability of the production process
Leading Indian steel producer Steel Authority of India (SAIL) has tasked Primetals Technologies with an upgrade of the process automation system at its Steckel mill in Salem, India. Primetals Technologies is responsible for the supply and implementation of Level 2 automation equipment and software.
Greater Accuracy and Reliability
The existing process automation system dates back to 1995. Conforming to the most modern standards, the new system provides operators with improved accuracy when controlling the rolling process. In addition, SAIL will benefit from increased mill availability. As a result, the modernization will enhance SAIL’s production of stainless steel at the Salem plant.
Execution During Planned Shutdown Periods
Automation experts from Primetals Technologies will implement the new system at the Steckel mill while the current Level 2 system is still in operation. The Primetals Technologies team will collect important values and insights related to mill configuration and the production process before switching to the new system. This allows for the implementation phase to be scheduled during planned shutdown periods. Moreover, the new process automation system will run on new hardware that dramatically reduces the need for IT-related maintenance.
Pioneering Indian Stainless Steel Market
The Salem steel plant is part of SAIL’s special steel branch, which has been pioneering the supply of wide-width stainless steel sheets and coils in India. The facility produces austenitic, ferritic, martensitic, and low-nickel stainless steel grades in the form of coils and sheets. The annual production of cold rolled items is at 340,000 tons while the hot rolling mill has a capacity of 364,000 tons per year. Moreover, the plant features India’s first state-of-the-art stainless steel blanking facility with a capacity of 6,600 tons of coin blanks as well as utility blanks and circles annually.
Primetals Technologies will modernize the Level 2 automation system at the Steckel mill in SAIL’s Salem plant.
- Bow-type caster with a capacity of 5,000 kilonewton per roll – equivalent to weight of 15 fully loaded trucks
- Will produce slabs of extraordinary thicknesses of up to 460 millimeters
- Startup scheduled for 2025
Wuyang Iron and Steel has placed an order with Primetals Technologies for a 1-strand continuous caster with several record-breaking features. The caster will be implemented at Wuyang’s plant in Wugang, Henan province, and is set to become the world’s most powerful of its kind. Moreover, it will produce the world’s thickest slabs, measuring up to 460 millimeters in thickness.
Thanks to the new equipment, Wuyang will be able to manufacture plates for heavy-gauge applications like the shipbuilding and wind turbine sectors. Annual capacity will be at one million tons of high-quality slabs. Products of such thicknesses are usually produced with ingot casters or vertical casters, both of which are not as cost-effective and efficient as Primetals Technologies’ new type of bow-type continuous slab caster.
Remarkable Reduction Force
Single Roll DynaGap (SRD) segments from Primetals Technologies allow for the dynamic alignment of individual roll gaps when changing parameters that influence the production, like steel grade, cooling grade, and casting speed. The SRD segments enable forces of 5,000 kilonewton per roll, corresponding to the weight of 15 fully loaded trucks. These extraordinary strong forces ensure sophisticated internal microstructures of the slabs, while keeping the mechanical properties at a consistent and high quality.
Unsteady Bulging Reduced by 50 Percent
The caster will also feature Primetals Technologies’ new and ground-breaking method for establishing ideal caster-roll geometry as early as at the design stage. This solution reduces unsteady bulging by 50 percent, enables higher casting speeds, and leads to greater productivity.
The tried-and-tested oscillator will be carefully designed with the philosophy of compensating for heavy weights by utilizing cascaded leaf springs, which helps to run the oscillator at dramatically reduced energy consumption levels.
Primetals Technologies’ continuous bending and straightening concept, Smart Segment, in combination with a dry-casting machine design that includes the Eco Star rolls results in significantly improved slab-surface quality. The Eco Star rolls’ internal cooling system is optimized to withstand the high temperatures needed to minimize surface defects during the dry-casting process.
A Leading Producer of Thick Plates
A subsidiary of HBIS Group, Wuyang Iron and Steel is leading the production of wide and thick steel plates in China. It also houses a key research centre within the steel plate industry. Wuyang Iron and Steel operates two technologically advanced, double-stand production lines for wide and thick steel plates.
Key facts: Wuyang Iron and Steel’s 1-strand slab caster
Capacity
1 million tons per year
Radius
12 meters
Metallurgical length
44 meters
Dimension of slabs
370 to 460 x 1,600 to 2,500 millimeters
Steel grades
low-carbon, micro alloyed, low alloyed, austenitic and martensitic stainless, peritectic, high-strength low-alloyed (HSLA)
- Primetals Technologies to upgrade power and electrical system at slab sizing press with new cycloconverter and low-voltage AC drives
- Modernization will ensure increased availability and future-proofed supply of spare parts
- Implementation scheduled for December 2024
Salzgitter Flachstahl , a subsidiary of the Salzgitter Group, has recently tasked Primetals Technologies with a comprehensive upgrade of its power and electrical system for the slab sizing press in its hot-rolling mill in Salzgitter, Germany. Primetals Technologies won this order following the completion of a successful crop-shear project at the same mill.
Increased Availability
The slab sizing press was designed to reduce pre-heated slabs in width, by up to 350 millimeters. The equipment’s drive technology is divided into two groups: the main drive, fed by a direct converter, and the supporting drivers, provided via DC-link converters featuring a common DC-link. This project will renew the converter technology for all the drives in both groups, and is aimed at increasing the availability of the production line while ensuring secured spare-part supply conditions for the power and electrical system.
The scope of supply encompasses a new cycloconverter for the main motor of the press, new low-voltage multi-drive DC-link converters for the pinch rolls and for gap adjustment, as well as implementation and startup services. The replacement of the drive systems will take place during planned standstill periods.
A Strong and Long-Lasting Partnership
Primetals Technologies and Salzgitter Flachstahl have collaborated on numerous projects over the last few decades, all the while building a strong and dependable relationship. As an example, Primetals Technologies recently improved the LD converter (BOF) process by executing a Level 2 automation upgrade, resulting in an optimization of lime quantities and an increased number of successful heats. Salzgitter Flachstahl is the largest subsidiary of the Salzgitter Group and produces hot-rolled strip, hot-rolled sheet, cold-rolled sheet, and surface-finished products at thicknesses from 0,4 to 25 millimeters and widths of up to 2,000 millimeters.
Salzgitter Flachstahl has invested in an automation upgrade from Primetals Technologies for a part of its hot-rolling line. Photo copyright: Salzgitter AG.
- Primetals Technologies has implemented a push-pull pickling line for strip thicknesses from 1.8 to 15 millimeters and process speeds of up to 200 meters per minute
- Enables a very wide product mix usually possible only with two conventional continuous pickling lines
- In-line skin-pass mill for enhanced control of strip flatness
Primetals Technologies has recently implemented the world’s largest push-pull pickling line (PPPL) at Chinese steel producer HBIS Tangsteel ’s steel plant in Laoting, Hebei province, China. The first pickled coil was successfully produced in December 2023. Primetals Technologies provided the full mechanical and electrics and automation scope and was responsible for engineering as well as advisory services for the implementation.
Extremely Wide Product Range
The core aim of Primetals Technologies’ push-pull pickling line is to enable an extraordinarily wide product range in terms of strip dimension, steel grade properties, and production capacity. This is normally achieved by operating both a conventional continuous pickling line and a PPPL in parallel. As a result, Primetals Technologies’ PPPL offers a clear advantage over conventional push-pull pickling lines from a flexibility perspective.
HBIS Tangsteel’s PPPL features an in-line 4-high single-stand skin-pass mill. A flatness control system adjusts the mechanical properties by allowing for controlled elongation. Thanks to the skin-pass mill, PPPL operators have even more control over strip flatness.
Maximized Throughput
Supported by an innovative solution for automated analysis and control of the pickling process, personnel at HBIS Tangsteel now have an extensive overview of all aspects of the process and are able to control it in a highly precise way. A part of the comprehensive Level 2 automation solution, the system is backed by a sophisticated pickling software model that considers numerous parameters related to the incoming strip. It was designed to ensure optimal operating conditions regarding temperature, pickling levels, flows, and turbulence. The application of the pickling model leads to a major increase in throughput capacity while ensuring optimal energy use and minimized consumption of pickling fluid.
The PPPL also features a turret-head-type side trimmer processing thicknesses from two to eight millimeters. This type of highly effective trimmer increases the throughput and maximizes strip-edge quality.
Ships to more than 100 countries
The backbone and largest steel subsidiary of HBIS, HBIS Tangsteel is one of the biggest state-owned iron and steel enterprises in China. The main products of Tangsteel are: hot-rolled and cold-rolled sheet, galvanized sheet, medium and heavy plate, as well as bar, wire, and section products, which are widely used in automobiles, appliances, machinery manufacturing, infrastructure, bridge construction, and other sectors. The products are shipped to more than 100 countries across the world. Tangsteel is committed to providing the most valuable steel materials and comprehensive service solutions for downstream businesses.
- Arvedi ESP line from Primetals Technologies centerpiece in transition of conventional production route into green steel manufacturing of hot-rolled strip
- Proven high quality of hot-rolled coil produced in endless mode as well as absence of fossil fuel consumption main reasons behind Zhongshou’s choice of technology
- Zero CO2 emissions during operation a further benefit for Zhongshou
Chinese steel producer Zhongshou Special Steel Group has recently ordered an Arvedi ESP line from Primetals Technologies for its plant in Luanzhou, Hebei Province. The festive signing ceremony took place in Vienna on April 17 and saw participation of top-level managers from both companies along with governmental representatives.
Primetals Technologies entities in Austria, China, and Germany will supply the complete mechanical scope as well as the process-related electrics and automation solution. The plant is scheduled to be in full operation at the end of 2025.
The Most Energy-Efficient Process
The Arvedi ESP endless strip production technology, acclaimed as the only officially certified solution for carbon neutral thin-slab casting and rolling, is the most energy-efficient process for producing endless hot rolled coil (eHRC) of high quality. This is the main reason why Zhongshou selected Arvedi ESP for its transition from the conventional route, consisting of an LD converter (BOF) and a hot-strip mill, into a production line based on an electric arc furnace (EAF) and Arvedi ESP.
“We have a clear target of holding a position as front runners in green steel production both on the domestic and international markets, while also being able to compete on markets protected by carbon border adjustment (CBAM) restrictions. The Arvedi ESP technology and its record-breaking low carbon footprint will be playing a key role for us in achieving this target,” says Zhongshou chairman Zheng Ting Wen.
“Currently, steel producers across the globe prepare to decarbonize their production routes. Zhongshou takes a decisive step on this endeavour with the investment in the world’s twelfth ESP plant, allowing the company to reach zero CO2 emissions at the casting-rolling stage during operation. We look forward to collaborating closely with Zhongshou in the transition to green steel production,” says Andreas Viehböck, Head of Upstream Technologies at Primetals Technologies.
“Almost 20 years ago, Giovanni Arvedi pioneered endless strip production with the invention of Arvedi ESP,” says Mario Arvedi Caldonazzo, CEO of Arvedi Group. “Today, after numerous improvements over the years, Arvedi ESP is still the only proven solution for green steel strip production. With this technology, Zhongshou Special Steel Group will be able to significantly reduce CO2 emissions while maintaining a high production capacity to meet the increasing need for highly demanding steel grades.”
Zhongshou’s ESP plant will be the 9th of its kind in China and is set to be the most powerful one on the market to date. This is thanks to its design, consisting of a long casting machine, four high-reduction mill stands, and five finishing mill stands. The plant will roll the freshly cast slabs starting at a strand thickness of 130 millimeters.
The high reduction capability will enable Zhongshou to supply the commodity market at high productivity rates, as well as high-strength low-alloy steel (HSLA) niches, including the automotive sector, with coil thicknesses ranging from 0.7 to 12.7 millimeters. The production will be geared towards full endless mode over the complete range of thicknesses.
Higher Levels of Productivity
The Arvedi ESP plant will incorporate advanced electrics and automation systems, featuring the latest Level 2 automation software models and technological control systems to achieve tight dimensional tolerances while ensuring exceptional product quality.
Moreover, automation solutions like Primetals Technologies’ anti-bulging solution LevCon will contribute to consistent and high levels of productivity. Arvedi ESP’s well-proven high throughput is made possible by the introduction of a new and innovative way of regulating the stopper. Additionally, thanks to LevCon, the casting speed is never slowed down to compensate for bulging effects.
3D rendering of Zhongshou’s Arvedi ESP line from Primetals Technologies.
- Large order of state-of-the-art process automation systems and technological packages, to be implemented at Rizhao Steel’s smart steel plant
- New solutions will enable a fully automated plant: “one-button steelmaking”
- Benefits for Rizhao Steel include improved product quality, productivity, and flexibility of production
Recently, Rizhao Steel has placed an order with Primetals Technologies to implement advanced process automation systems and technological packages at its integrated steel plant in Rizhao, China. Powerful metallurgical models, dynamic process control systems, and detailed calculations of input materials will enable full plant automation, “one-button steelmaking”, from a central control station.
Thanks to a high level of autonomous operation, the Chinese steel producer will benefit from improved product quality, higher productivity, as well as improved production flexibility. Moreover, operators at the Rizhao plant will get valuable insights from production data. This project underscores Rizhao Steel’s intention to become one of the leading steel producers in China in terms of automation excellence.
Fully automated plant
Primetals Technologies will install comprehensive process optimization solutions and technological packages across Rizhao Steel’s production facilities, including three LD converters (BOF), four twin ladle furnaces, and two twin RH plants. The scope also includes a state-of-the-art system for the monitoring and analysis of process gas.
The Level 2 automation solutions for the meltshop feature tried-and-tested automation-related aspects such as data management of materials, steel grades, and production planning. This integration ensures a highly automated and standardized production process, enabling a fully automated plant controlled from a central control station, i.e. steelmaking at the push of a button, an innovative approach that minimizes the need for operators to interfere in the production process, while at the same time maximizing operational efficiency and consistency.
Autonomous operation
The technological solutions provided by Primetals Technologies are designed to ensure that Rizhao will meet several key objectives with its smart plant. This will be realized, for example, by limiting the occurrence of manual processes such as oxygen lance height adjustment, by providing operator guidance based on meticulous calculations for all process steps, and by standardizing production processes across all work shifts. The implementation of a number of intelligent modules from Primetals Technologies, like the BOF Optimizer, LF Optimizer, and RH Optimizer, will competently support the production process, ensuring efficient decision-making and ongoing improvement of production processes. The result is a highly effective, quality-focused production environment that will put Rizhao Steel on track to become a leader in smart steel production in China.
Rizhao Steel, founded in 2003, is a company of the Rizhao Steel Holding Group, located about 30 kilometers outside Rizhao Port in the south of Shandong Province. The steel producer has an annual crude steel output of 15 million tons and employs some 16,000 people. Its product portfolio includes hot-rolled coils, wire, bars, and small I-beams, which are mainly sold to Chinese customers.
Rizhao Steel holds a leading position in the Chinese steel industry, not the least due to the implementation of the energy-efficient Arvedi Endless Strip Production (ESP) technology, supplied by Primetals Technologies.
Primetals Technologies’ automation and digitaliztion solutions will enable “one-button steelmaking” for Rizhao Steel’s fully integrated steel plant.
The extensive Level 2 automation solution from Primetals Technologies will result in improved product quality, higher productivity, and improved production flexibility.
- Primetals Technologies Japan’s green steel office relocated
- Establishes new engineering office in Tokyo to ensure swift technical support
Effective April 1, 2024, Primetals Technologies Japan relocates its green steel office from Hiroshima to Tokyo. As part of a strategic move to strengthen the presence in Tokyo, Primetals Technologies also opens an engineering office in the capital.
Close collaboration on solutions for green steel
Primetals Technologies Japan’s local green steel office specializes in supporting steel producers that seek to decarbonize their ironmaking and steelmaking production lines. Primetals Technologies is the market leader in environmental and energy-efficiency solutions for the metals industry and has established an organization dedicated to the transformation into a greener steel industry. The green steel office in Tokyo collaborates closely with the larger green steel organization as well as other entities across the globe.
Solutions for green steel production attracts more and more interest. Thanks to the green steel office’s new location, Primetals Technologies is able to closely collaborate with research and development departments of several leading Japanese steel producers on projects related to new and greener production routes.
Swift technical support
There is also an imminent need for swift and smooth technological support in the larger Tokyo metropolitan area, and therefore, Primetals Technologies establishes an engineering office in the capital of Japan. Personnel from the Hiroshima office are relocated, and the new office will also include newly hired personnel. As part of the strategically planned changes, the former Tokyo sales office is renamed as the Tokyo office, underlining the reinforcement of Primetals Technologies’ presence in Tokyo.
Primetals Technologies Japan’s main business areas comprises downstream equipment including but not limited to development, design, manufacture, and service of solutions for hot rolling, cold rolling, processing, and continuous casting.
Primetals Technologies Japan enhances its collaborations with steel producers in Japan with the strategic relocation of the green steel office and the establishment of a new engineering office in Tokyo. Pictured here is a rendering of Primetals Technologies HYFOR and Smelter solutions to the right as well as an electric arc furnace based plant to the left.
• LiquiRob robotics system from Primetals Technologies designed for a new approach toward safe and efficient shroud manipulation
• Advanced 3D camera system ensures exact positioning
• Improved occupational health for operators
Thai steel producer Siam Yamato Steel has realized a new robotic concept from Primetals Technologies, including LiquiRob, at its steel plant in Map Ta Phut. The solution is used for shroud manipulation at Siam Yamato Steel’s bloom caster. References from recent robotics system projects and the tailormade technological solution were among the decisive factors influencing Siam Yamato Steel’s choice of supplier.
Thanks to the robotics solution, safety and occupational health have improved significantly at the steel plant. Workers operating the shroud manually previously had to stand right next to the tundish and the flow of liquid steel coming from the ladle. Additionally, in the event of a so-called “frozen ladle” i.e. an unwanted solidification of liquid steel in the ladle, operators had to get into even closer proximity of the ladle slide gate to manually execute oxygen lancing.
Performing dangerous tasks
Developed by Primetals Technologies, the new concept consists of a standard ladle shroud manipulator equipped with a mechanical interface tailored to Siam Yamato Steel’s needs. The robot attaches to the interface to guide the shroud in the right position and attach it to the ladle. Primetals Technologies’ position measurement system, featuring a 3D camera system, determines the correct position of both the ladle and the shroud manipulator. The LiquiRob robotics system performs several dangerous tasks, including oxygen lancing, tundish measurements, tundish sampling, and tundish powder feeding.
Increased safety for operators
Primetals Technologies has also devised and executed a comprehensive safety concept as part of the LiquiRob robotics solution at Siam Yamato Steel. A fence that encloses the area near the robot as well as doors with automated safety locks ensure that the surroundings are secured before the LiquiRob robot system starts operating, elevating occupational safety at the plant.
Primetals Technologies’ scope of supply comprised a LiquiRob robotics system, a tailormade shroud manipulator, a camera system, electronics and automation equipment for automated operation, and a pneumatic cubicle.
Meeting domestic needs
Established in 1992, Siam Yamato Steel produces hot-rolled structural steel. It operates two plants in the industrial estate of Map Ta Phut with a total annual production capacity of 1.1 million tons of steel. The domestic need for heavy section steel is almost entirely met by the production output of Siam Yamato Steel, the company therefore makes a significant contribution to Thailand’s economy.
LiquiRob is a registered trademark of Primetals Technologies in certain countries.
The new tailormade LiquiRob robotics system from Primetals Technologies, in operation at Siam Yamato Steel’s plant in Map Ta Phut.
• Primetals Technologies to upgrade automation systems at hot-strip mill
• Shadow mode ensures smooth switchover to new system and a minimized shutdown period
• Advanced control system for more precise calculation of values at final rolling and coiling stages
Chinese steel producer Shougang Qianan has recently chosen Primetals Technologies for a comprehensive upgrade of the automation systems at its hot-strip mill in Qianan, Hebei province. The new systems are scheduled to be in operation by May 2025.
Improved accuracy during rolling
Numerous references across the globe and the fact that Primetals Technologies continually refines the technology are two of the main reasons behind Shougang Qianan’s choice of supplier. The process optimization system (Level 2) from Primetals Technologies will allow the Chinese producer to meet and exceed the requirements of demanding applications like electrical steel and strip for the automotive industry. It enables more accurate control of strip temperature, profile, and thickness during the rolling process.
Shadow mode for smooth system exchange
Primetals Technologies will supply and implement a new state-of-the-art Level 2 automation system and upgrade specific functions of the Level 1 automation system. Switching to the new systems will be a smooth and swift process, thanks to a so-called shadow mode. The team from Primetals Technologies will connect the new system to the mill environment while the current system is still in operation. This approach ensures that the implementation team receives valuable configuration settings and insights related to the production process before the shutdown itself takes place. Moreover, self-learning neural networks, i.e. the process models, leverage the process data, further ensuring a safe changeover to the upgraded Level 2 system.
Optimized rolling speed and temperature
A part of the Level 2 automation system, the Comprehensive Temperature Control (CTC) model optimizes rolling speed and temperature, which results in improved plant performance. The model uses temperature values from a measuring point located after the roughing mill to predict rolling temperatures. It controls the speed of the finishing mill with an optimized speed diagram – a database of settings for achieving the correct speed in a vast array of production conditions.
Shougang Qianan is a subsidiary of the Shougang Group. Its portfolio comprises the complete range of cold and hot-rolled steel products, including electrical steel, automotive, pipeline, and sheets for the home appliance industry, as well as value-added services.
Shougang Qianan has chosen Primetals Technologies for a comprehensive automation upgrade of its hot-strip mill in Qianan, Hebei province, China.
- SSAB places additional order for comprehensive millstand modernization after successful upgrade of stand No. 1
- Complete drive system at tandem cold mill to meet most modern standards
- Equipment scheduled to be fully implemented by May 2026
In early Spring 2023, Primetals Technologies implemented millstand drives for stand No. 1 at SSAB ’s 4-stand tandem cold rolling mill in Hämeenlinna, Finland. Phase 2 of the millstand drive modernization was executed in late 2023, and recently, Primetals Technologies received the final acceptance certificate (FAC) from SSAB. Following the successful Phase 1 and 2 projects, SSAB has now tasked Primetals Technologies with Phase 3 to 5 of the upgrade.
A smooth integration of new systems
During Phase 1 of the modernization, Primetals Technologies upgraded the complete drive system, including transformers, drive, and motor, for millstand No. 1. Primetals Technologies’ execution of the project met SSAB’s expectations, and the Finnish steel producer also appreciated the smooth merging of new and existing systems. SSAB placed the follow-up order shortly after the completion of Phase 1.
Increased availability of tandem cold mill
In Phase 3 and 4 the transformers, drives, and motors of the remaining mill stands will be modernized in a similar way to Phase 1 and 2. In Phase 5 an obsolete motor will be refurbished, allowing it to be used as a replacement for the other already modernized motors. The objective of the extensive upgrade is to secure the supply of spare parts for the millstand drives well into the future. Moreover, the availability of the tandem cold rolling mill will be increased.
SSAB Hämeenlinna and Primetals Technologies have collaborated on several successful projects over the last few years, including a modernization of the Level 2 automation system at the tandem cold rolling mill in 2022 and a modernization of the Level 1 automation system at the same mill in 2017. The most recent projects underscore the close partnership between the two companies.
Steel for ultra-high-strength safety structures
Established in 1972, SSAB Hämeenlinna employs some 1,000 people. The 4-stand tandem cold rolling mill produces coil ranging from 660 to 1,575 millimeters in width at thicknesses of 0.35 to 3.1 millimeters. In Hämeenlinna, SSAB manufactures cold-rolled as well as metal- and color-coated steel in the form of coils, precision tubes, hollow sections, strip, and slit strip. The items are used for a wide array of applications in sectors like automotive – for example, in the form of ultra-high-strength safety structures in cars – construction, or household appliance manufacturing.
SSAB Hämeenlinna has placed a follow-up order with Primetals Technologies for a modernization of the millstands at its cold rolling mill in Hämeenlinna, Finland. Photo of the steel producers’ tandem cold rolling mill. Copyright: SSAB Hämeenlinna
- Complete wire rod mill with state-of-the-art mechanical and automation technology
- New generation of No-Twist Mill (NTM) with individually driven stands
- First Morgan Rod Reducing/Sizing Mill (RSM) in Turkey compatible with the tight tolerance requirements in the high carbon tire cord market
- Long rolling (LR) Process Expert, a comprehensive modular Level 2 automation solution, optimizes production processes
- From first hot coil to final acceptance of contract within 20 days
Primetals Technologies has received the final acceptance certificate (FAC) for a wire rod mill modernization project at Kaptan Demir Çelik (Kaptan Iron & Steel, part of Kaptan Group) in Marmara Ereğlisi, Turkey. With an annual capacity of 650,000 tons, the facility will process carbon, austenitic stainless steel, and cold heading grades.
The project has expanded Kaptan’s portfolio to include such value-added products as coiled rebar, fine grain rebar, and welding wire for the engineering and automotive industries in both domestic and export markets. The new equipment allows Kaptan to be a quality leader on the world market.
Setting a new standard
The startup was remarkably quick. It took only 21 days from start of hot commissioning until the first saleable product. This record-setting implementation has established a new industry standard and was made possible thanks to an experienced project team as well as close and effective collaboration between Primetals Technologies and Kaptan Demir Çelik.
The equipment’s technological advantages, along with prominent aftermarket services, ensured by Primetals Technologies’ local presence in Turkey, were two of the main influencing factors when Kaptan chose Primetals Technologies as supplier in 2021.
Consistently high quality at lower energy costs
The new wire rod outlet has increased Kaptan’s overall production and finishing speeds. The mill rolls up to 105 tons per hour at speeds of up to 110 meters per second. Kaptan can now offer quality carbon products ranging from 4.5 to 26 millimeters in diameter at an expanded range of rebar sizes from 6 to 20 millimeters.
Kaptan’s new mill has the distinction of being the first to combine a Morgan Rod Reducing/Sizing Mill (RSM) with a next-generation No-Twist Mill (NTM) consisting of individually driven stands. This configuration allows Kaptan to consistently deliver high-quality finished products at reduced alloying and energy costs. The RSM can also achieve the tight tolerances required for the high carbon tire cord market. Additional production advantages result from a metallurgical in-line heat treatment process using high-precision Morgan Water Boxes and Morgan Stelmor Controlled Cooling Conveyor.
Streamlined operations
Primetals Technologies’ electrical and automation supply included the main and auxiliary drives and motors, new Level 1 automation system with human-machine interface (HMI), new Level 2 Process Expert automation, as well as the central and local operator stations.
A state-of-the-art Level 1 automation solution from Primetals Technologies helped to minimize the total shutdown period of the wire rod mill and to realize a fast and easy production ramp-up. Using a tablet-style mobile control panel from Primetals Technologies, operators can safely control local equipment for inspection, adjustment, and other maintenance-related tasks.
The automation scope is rounded off by a cost-effective Level 2 process automation system. The Long Rolling (LR) Process Expert, developed by Primetals Technologies, is a platform for production management. Modules can be added to provide insights into material tracking and quality control. They are based on actual production data. The system features a simple interface to evaluate plant performance and to execute production process related optimization measures. Together, these systems pave the way for greater interconnectivity and more effective plant management.
The project scope also includes operating parts, guide equipment, offline devices for stand preparation, media systems, engineering services for other components, advisory services for construction and implementation, and training of personnel.
Ships to more than 100 countries
Kaptan Demir Çelik began production on its first rolling mill in 1964 and continues to expand its presence at Marmara Ereğlisi. Kaptan’s products are used in more than 100 countries worldwide. With this reach, they have put themselves in pole position to lead the European market.
NO-TWIST, RSM, and Stelmor are registered trademarks of Primetals Technologies in certain countries.
- Steel Authority of India Limited (SAIL) and Primetals Technologies to collaborate on green steel projects and technology at steel plant in Rourkela, India
- Important strategic move for the evaluation of decarbonization solutions across integrated steel plant portfolio
On February 20th, Primetals Technologies and leading Indian steel producer Steel Authority of India Limited (SAIL) signed a Memorandum of Understanding (MOU) to closely collaborate on projects and technologies related to decarbonization at the plant located in Rourkela, Odisha, India. The signing ceremony took place at the executive director’s office of SAIL’s Rourkela Steel Plant.
SAIL’s Rourkela steel plant has a strong focus on decarbonization as one of its priorities in order to future-proof the production processes, and is therefore currently looking for solutions to lower its carbon footprint. The partnership with Primetals Technologies is a key strategic move in this endeavour.
A full-fledged provider of green production solutions
Primetals Technologies is the market leader in environmental and energy-efficiency solutions for the metals industry and has established an organization dedicated to green steel technologies and the transformation into a greener steel industry. Primetals Technologies will work closely with SAIL’s Rourkela location, providing expertise across the green ironmaking and steelmaking value chain, including but not limited to carbon capture and utilization (CCU), digitalization, hydrogen-based steel production, electric steelmaking, and advanced gas-cleaning solutions.
Leading plant building expertise
“We are very happy to partner with SAIL and the Rourkela steel plant for its transition into green steel production,” said Norbert Petermaier, Executive Vice President of Sales at Primetals Technologies. “The metals industry is currently moving quickly in terms of efforts to decarbonize. As the global front runner, Primetals Technologies will support and assist the SAIL Rourkela steel plant in the best possible way based on our proven expertise in green ironmaking and steelmaking solutions. And, as part of the larger Mitsubishi Heavy Industries Group, we also have at our disposal profound knowledge in technologies related to carbon capture and utilization.”
“The SAIL Rourkela steel plant is happy to get associated with Primetals Technologies on our endeavor to cut down the carbon emissions in order to meet our overall target of becoming net-carbon neutral,” said Sharad Raghunath Suryawanshi, Executive Director (Works) of SAIL’s Rourkela steel plant, on the occasion of the MOU signing ceremony.
The SAIL Rourkela location is a leading steel plant in India and the world. The Rourkela facility alone has an annual crude steel capacity of 4.2 million tons. The plant’s product portfolio is wide-ranging and comprises: prime plates, hot rolled coils, cold rolled coils and sheets, galvanized sheets, cold rolled non-oriented (CRNO) electrical steel, electric resistance welded (ERW) pipes, spiral welded pipes, and special plates to serve the defense sector.
Biswadeep Bhattacharjee, Vice President of Sales and Head of Green Steel India at Primetals Technologies, and Sharad Raghunath Suryawanshi, Executive Director (Works) at SAIL’s Rourkela steel plant, during the contract signing ceremony.
- 20-high HZ-mill from Primetals Technologies will enable Anshan Iron and Steel Group to realize grain-oriented silicon steel grades of exceptional structural quality
- Strategic investment allowing the producer to benefit from the rapidly growing market of electric vehicles
Recently, Primetals Technologies was selected by Chinese steel producer Anshan Iron and Steel Group to supply a reversing cold mill for its steel plant in Anshan City, Liaoning province. The new 20-high HZ-mill will produce high-strength silicon steel for the fast-growing electrical steel market.
Increased productivity
The HZ-mill, an advanced split-housing ZR-mill from Primetals Technologies, has several benefits over a conventional ZR mill. For example, the HZ-mill is designed with a large gap opening, which results in easy strip threading and a smooth recovery after strip breakages. Moreover, the roll-diameter configuration is tailored to individual needs, and the HZ-mill features a Double AS-U shape control system for a stabilized rolling process and an increase in productivity.
The HZ-mill lets operators utilize almost the entire range of the work rolls, regardless of the diameter of the intermediate rolls. This results in more options – another advantage over the monoblock ZR-mill.
A leading supplier
A regional subsidiary of parent company Ansteel, Anshan Iron and Steel Group has a comprehensive product portfolio that includes hot-rolled sheet, cold-rolled sheet, galvanizing sheet, color-coating sheet, cold-rolled silicon steel, heavy rail, seamless pipe, section, and construction steel. Anshan is the leading supplier of steel to the automotive, bridge, and nuclear power industries in China. Additionally, Anshan holds an important position in the markets for railway products, home applicants, and steel for the energy industry.
Representatives from Ansteel and Primetals Technologies during the contract signing ceremony for the 20-high rolling mill.
- Manufacturing execution system (MES) ensures smooth and future-proof operations
- Closes gap between enterprise resource planning (ERP), scheduling, and automation systems
- Further benefits for Hoa Phat include greater process transparency, an automated data flow, and efficient production management
Leading Southeast Asian steel producer Hoa Phat Dung Quat Steel has recently chosen Primetals Technologies for the implementation of a manufacturing execution system (MES). The new software will manage production orders and material properties across the new production lines at the integrated steel plant in Dung Quat, Quang Ngai Province, Vietnam. The result is enhanced operational efficiency thanks to the software enabling faster and more efficient processing of data and handling of information related to the production process.
“The MES relieves workload from operators, as certain manual tasks, such as inputting pieces of information from the order system into the production management system, are no longer needed. The system also protects Hoa Phat from the loss of production data,” says Louis Deaulmerie, Sales and Project Manager at Primetals Technologies.
Holistic and highly flexible
By the end of 2025, Primetals Technologies will have implemented new production lines for Hoa Phat consisting of two slab casters, one hot-rolling mill, modern automation systems, and comprehensive digitalization solutions. The MES will handle production orders, process instructions, and production data across the entire extended part of the steel plant. Additionally, thanks to the use of standard interfaces, the new system can be integrated into the existing process optimization systems from Primetals Technologies as well as 3rd party automation and software suppliers.
The project will be executed by specialists from several entities across Primetals Technologies’ global organization. As a software platform, they will be using the industry-leading PSImetals solution, which will be regularly updated and upgraded to keep its edge well into the future.
The largest steel producer in Southeast Asia
Hoa Phat is the leading industrial manufacturing group in Vietnam. Currently, the company operates in five sectors: iron and steel (construction steel and hot-rolled coil), steel products (including steel pipes, galvanized steel, drawn steel wire, pre-stressed steel), agriculture, real estate, and home appliances. Steel production is at the heart of the business, accounting for 90 percent of its revenue.
The largest steel producer in Southeast Asia, Hoa Phat boasts an annual capacity of eight million tons of crude steel. In 2021, Hoa Phat placed an order at Primetals Technologies for a greenfield project including two continuous casters and one rolling mill as well as process control and optimization software, the intelligent digital assistant Asset Life Expert (ALEX), caster and hot-rolling mill scheduling and the integrated digital knowledge-based quality control system Through-Process Quality Control (TPQC).
The production management system pre-project team consisting of experts from Hoa Phat, Primetals Technologies, and PSI Metals.
- Intermediate cooling unit will be supplied and installed at Hyundai Steel in South Korea
- Technology will increase mill productivity by reducing overall processing time
- Implementation scheduled for October 2024
Recently, Primetals Technologies received an order from Hyundai Steel for the installation of a new intermediate cooling (IC) technology at its heavy plate mill line located in Dangjin, South Korea. The cooling unit will be installed between the roughing mill stand and the finishing mill stand. This enhancement will substantially increase the mill’s productivity, enabling the production of high-quality steel plates tailored to the most demanding markets, including the shipbuilding and oil and gas industries.
Primetals Technologies will be responsible for the design, engineering, equipment supply, installation, training, and commissioning of the IC unit, including electrical, automation, and related fluids equipment.
Intermediate cooling technology
The IC unit is 12 meters long and will incorporate side sweep sprays, air blow offs, and cooling stations. Positioned after the roughing mill exit table, this unit employs a total of eight top and eight split-bottom stainless steel cooling headers. The possibility of controlling the number of headers in use and the unit’s accurate speed control deliver the desired cooling intensity, which is tailored to each individual product.
The automation systems supplied as part of the technology package include Level 1 and Level 2 automation, ensuring efficient monitoring and control of the water supply to the cooling headers from the overhead tank. The IC technology guarantees precise cooling for the transfer bars as required by the production strategy.
Increased mill productivity
When processing a steel plate on a 2-stand mill, the plate is transferred from the roughing mill stand to the finishing mill stand for the final rolling step. Depending on the process parameters, the transfer time is deliberately extended, creating a pause in the rolling sequence. This pause, known as the hold time, can account for a significant portion of the total production time for a single plate, leading to reduced mill utilization.
The new cooling system, positioned after the roughing mill, will efficiently decrease the overall hold time of the plates or transfer bars between the stands, thereby reducing the processing duration for a single plate. This enhancement significantly boosts mill productivity.
A global player in steel production
Hyundai Steel is one of the world’s leading steel companies, equipped with both blast furnace and electric arc furnace production facilities. Established as Korea’s first steelmaker in 1953, the company has championed sustained success by boosting its blast furnace business as a new growth engine alongside its established electric arc furnace-based operation. Its industry-leading product portfolio encompasses steel plates, sheets, structural steel, coils, steel casting products, and H-sections, catering to the most demanding sectors including automotive, shipbuilding, offshore structures, railways, and construction.
A 3D image of Hyundai Steel’s intermediate cooling unit from Primetals Technologies.
- Upgrade of 40-ton AOD converter shop results in increased productivity, improved product quality, and increased lifetime
- Startup scheduled for beginning of 2025
Italian special stainless steel producer ASONEXT has tasked Primetals Technologies with the revamp of its 40-ton argon-oxygen decarburization (AOD) converter shop at its facilities in Brescia, Italy. Primetals Technologies previously executed a comprehensive study for ASONEXT on the existing AOD process. The study provided the steel producer with certain pieces of advice that are already resulting in a significant improvement to the production process. As part of the study, Primetals Technologies proposed the revamp of ASONEXT’s AOD converter, which is now about to be realized.
Well-established AOD expertise
As the leading provider of AOD equipment, Primetals Technologies has supplied the majority of the world’s AOD plants. Tried-and-tested expertise related to the AOD process as well as the sound reference base were two reasons behind ASONEXT’s choice of supplier. The startup of the new converter is scheduled for the beginning of 2025. Primetals Technologies is responsible for the engineering, scope of supply of production equipment, and supervision of construction work and implementation.
New geometry results in productivity boost
ASONEXT is targeting small production lots of special stainless steel grades and alloys for high-tech applications. This niche poses a challenge to the production process, including the performance of the AOD converter. Primetals Technologies will design a new type of vessel geometry, resulting in a 30-percent increase of the inner vessel volume. This, in turn, ensures improved vessel lining performance and a 12-percent improvement of the reaction volume. Moreover, a new design of the detachable, reinforced top cone will result in a longer lifetime as well as smoother and more streamlined maintenance. A further benefit for ASONEXT is a productivity boost, which is a result of shorter treatment times.
Established in 1971, ASONEXT has an annual production capacity of 150,000 tons. The Italian producer serves several markets including the aerospace, ship building, and petrochemical industries.
The revamped AOD converter from Primetals Technologies ensures increased productivity.
- Largest twin-station vacuum-tank degasser in North America will produce cleaner steel
- Extensive upgradeof 2-strand continuous caster to result in improved internal slab quality
- Exceptionally short downtime of 30 days for the slab caster upgrade
Primetals Technologies and JSW Steel U.S.A. have entered into an agreement to upgrade the slab casting infrastructure at its Mingo Junction, Ohio, plant. The project encompasses steelmaking, secondary metallurgy, and continuous casting processes, and the project is expected to enable JSW Steel U.S.A. to produce a wider range of sophisticated steels in the form of slabs to diversify its product portfolio for additional markets.
Work on the project has begun and is scheduled for completion in second half of 2025.
Installing largest vacuum tank degasser in North America
Primetals Technologies will install a 230-ton vacuum tank degasser (VTD) with a dry mechanical vacuum pump system. This will be North America’s largest VTD to date, allowing JSW Steel U.S.A. to produce cleaner steel and reduce levels of carbon, oxygen, nitrogen, hydrogen, and sulfur in different process steps.
“JSW Steel U.S.A. wanted to install this VTD at their existing Mingo Junction site with significant footprint and height restrictions,” said Joerg Buttler, Head of Upstream Business for Primetals Technologies U.S.A. “Working closely with JSW’s Mingo team, we were able to create a custom design that worked for the space, budget, and metallurgical targets.”
The VTD design includes all the mechanical and electrical equipment for the plant, including the mechanical dry pumps, vacuum filters, and dust catcher. It includes integrating new material handling technologies, associated auxiliary systems, metallurgical process model, and complete Level 1 and Level 2 automation systems.
“We look forward to the successful completion of these upgrades to strengthen our service capabilities and meet the growing needs of the renewable energy and infrastructure markets while staying in line with the Build America - Buy America Act (BABAA),” said Jonathan Shank, Chief Operating Officer of JSW Steel U.S.A.’s Mingo Junction plant. “The project will strengthen our commitment to sustainability while providing additional momentum for growth by widening our product portfolio.”
Remarkably short downtime for caster upgrade
For the 2-strand continuous caster upgrade, the project scope includes key mechanical equipment, Level 1 automation for strand No. 2, a complete Level 2 automation system, and the mold-monitoring system Mold Expert. Moreover, JSW Steel U.S.A. has signed up for a long-term software subscription model, based on a software as a service (SaaS) concept.
Revamping a continuous slab caster usually results in a shutdown period of several months. However, in this project, Primetals Technologies managed to cut the downtime to 30 days. This timeline is possible by keeping the existing concrete foundations and strand supporting structure, which renders any time-consuming demolition work unnecessary. The new strand containment will be fixed with a specially designed adapter solution, which is another important factor leading to the short downtime.
A patented continuous bending and straightening process, Smart Segment allows for online and remote adjustments of the roll-gap at one of the strands. This strand will be dedicated to producing API grades and plates of high quality for the US market. The Smart Segments parameters are set based on advanced mathematical models developed by Primetals Technologies. These models ensure that the caster already at the design phase is optimized to eliminate the risk of unsteady mold level bulging.
Models for quality improvements
Having real-time knowledge of the exact temperature of any section of the continuous casting strand is highly valuable for achieving fully optimized secondary cooling of the slabs. This is made possible with Dynacs 3D, a secondary-cooling model for the adjustment of cooling setpoints. Additionally, the model calculates the point of final strand solidification, which enables exact control of the cooling process. The caster will also be equipped with DynaGap Soft Reduction 3D, a dynamic soft-reduction package that gives operators precise control during slab solidification and significantly improves internal slab quality by reducing center segregation. DynaGap is a strand-guide system, allowing operators to adjust the roll gap at the push of a button.
Key facts
JSW Steel U.S.A.’s new vacuum tank degasser
- Plant type: twin type vacuum degasser with movable vessel car and fixed and liftable cover
- Capacity: 230 tons
- Major Equipment: vacuum filter, dust catcher, set of dry mechanical pumps, and associated material handling system
JSW Steel U.S.A.’s new slab caster
- Thicknesses: from 228.6 to 304.8 millimeters
- Widths: from 991 to 2,032 millimeters
- Radius: 10.5 meters
- Metallurgical length: 26.45 meters
Automation systems subscription model
- JSW Steel U.S.A. receives new releases, upgrades, and updates on a regular basis
- The service package included in the annual license fee also features remote support for troubleshooting, advice, training, fine-tuning, or optimization
- The automation systems stay compatible with the latest hardware and operating systems, new functions can easily be integrated in future, and capital investments are replaced by annual operating expenses
- Utilizes advanced mathematical methods for next-level caster design optimization
- Reduces unsteady bulging by 50 percent
- Allows for higher casting speeds and greater productivity while producing slabs of reliable and high quality
For decades, Primetals Technologies has been refining the roll geometry of continuous casting machines, resulting in an increasingly stable mold level during the casting process. The most recent development is a ground-breaking model for establishing the ideal caster roll geometry already at the design stage.
Casting at higher speeds
This solution allows for a preview of how the caster will perform during operation, as it simulates both the unsteady bulging effect and mold level fluctuations caused by the phenomenon of bulging. The model enables steel producers to implement new or revamped casters that are designed to minimize mold level fluctuations during production. Therefore, they will be able to cast at higher speeds while producing slabs of high metallurgical quality.
A stable process during continuous casting is essential to produce high-quality products. Bulging is common and occurs as liquid steel at the core of the hot strand pushes against the shell of the slab as the strand moves between two rolls. During this process, heavy fluctuations in the mold level can build up, which might cause surface defects, or, in a worst-case scenario, a breakout, in which liquid steel pours out of the shell. Intensified bulging often results in operators having to reduce the casting speed.
Greater stability and product quality
Unsteady bulging is a complex problem involving, among other factors, mold level deviations, solidification in the mold, and shell growth in the secondary cooling zone. The newly developed model is designed to consider all these parameters. Utilizing Fourier transform, an advanced mathematical method, Primetals Technologies’ innovative software tool is capable of including a wide spectrum of parameters such as targeted steel grade, section size, and casting speed in its calculations. In this way, it identifies just the right frequency spectrum needed to set the optimal roll geometry.
Unsteady bulging reduced by 50 percent
Thanks to these simulations, it is possible to optimize the distance and diameter of the rolls before installing the equipment. Roll pitches are one of the main factors causing unsteady bulging, and by optimizing roll geometry, unsteady bulging is reduced by about 50 percent. Over the last months, this remarkable achievement was accomplished repeatedly at several steel plants where this solution is already implemented.
There are more benefits to be had with the new software model. Minimizing the occurrence of unstable bulging increases the caster’s range to include peritectic and ferritic steel grades, as no reduction in casting speed is necessary. Moreover, smoother strand shells and increased slab-surface quality are ensured.
The optimization of the rolls can be executed also for existing casters implemented by other plant builders.
Primetals Technologies has developed a solution to optimize the continuous casting process by adjusting the distance and diameter of the rolls already before implementing the machine.
This graph visualizes the great discrepancy in stability between non-optimized and optimized casters, as it shows mold level deviation in a continuous caster before optimization (left side) and after optimization by Primetals Technologies (right side). The discrepancies are shown in the upper graph on both sides of the standard deviation curve indicated in red.
- Primetals Technologies to supply EAF Ultimate with an annual capacity of 1.6 million tons of liquid steel
- Comprehensive automation system enables detailed process control and calculation of carbon footprint
- Huge step for the production of green steel in Austria
voestalpine has placed an order with Primetals Technologies for a 180-ton EAF Ultimate to be implemented at the Austrian steel producer’s site in Linz, Austria. Startup is scheduled for 2027. The EAF Ultimate will be playing a key role in voestalpine’s green transition program “greentec steel.” As a first step in this ambitious decarbonization program, one electric arc furnace will be built at each of voestalpine’s sites, in Linz and Donawitz.
Latest generation of EAF based steelmaking plants
Primetals Technologies will supply the complete EAF Ultimate equipment, a dedusting system, a waste-heat recovery system, electrical grid stabilization, and material handling for alloying materials and additives. The order also includes full Level 1 and 2 automation, a power supply system including a static synchronous compensator (STATCOM) for optimized grid stabilization, and the LiquiRob robotic system, which increases efficiency and occupational safety at the plant.
The EAF Ultimate will be designed to incorporate industry-leading solutions for environmentally friendly steel production. For example, the heat recovery system will convert much of the waste heat into steam, which is then fed back and used in other production units.
“We are very happy to strengthen our close and long-lasting partnership with voestalpine and to support them on their way to becoming CO2-neutral. The EAF Ultimate is part of our latest generation of electric steelmaking plants and is well-known for its raw material flexibility, fully automated operation, advanced control systems, and environmental efficiency. With this technology, voestalpine is set for a future of decarbonized steel production,” says Andreas Viehböck, Head of Upstream Technologies at Primetals Technologies.
In August 2022, Primetals Technologies announced a significant contribution to Salzgitter’s SALCOS green steel transition project in Germany. This collaboration and other recent references as well as expertise in both the production of advanced steel grades and leading automation solutions were the most important factors influencing the decision to choose Primetals Technologies as the supplier for the new electric arc furnace and meltshop equipment.
State-of-the-art automation system
The automation scope includes the latest generation of the web-based DCS process control system, which unites the engineering and operational teams in the same environment. This system ensures intuitive system operation and best-in-class support in maintenance-related topics. The Level 2 automation system is state-of-the-art, resulting in superior process control and the possibility to calculate the carbon footprint of the electric steelmaking plant.
Global market leader
Headquartered in Linz, Austria, voestalpine is a global steel and technology group and a leading partner to the automotive and consumer goods sectors as well as the aerospace and oil and natural gas industries. The company is also the global market leader in railway systems, steels for the manufacture of tools, and special sections. voestalpine is committed to global climate goals and has a clear plan for decarbonizing steel production via its greentec steel program.
The EAF Ultimate is equipped with various features to increase the degree of automation, boost productivity, and contribute to increased safety for operators.
- Hot edge inductors supplied as upgrade to existing S5 cold mill line to enhance rolling capability
- Enables the mill line to improve product quality, meeting the demands of the can packaging market
- Implementation of edge inductors scheduled for first quarter of 2024
Recently, Primetals Technologies received an order from Hulamin for the addition of hot edge inductors as part of an upgrade to its current aluminum cold rolling mill in Pietermaritzburg, South Africa. This upgrade will address strip issues such as tight edges. The enhancement will allow the plant to achieve excellent product quality and improve the overall rolling capability. Primetals Technologies will be responsible for the design, procurement, manufacture, supply, and implementation of the inductor system.
Effective flatness control system
The function of the hot edge inductors is to apply heat to the work rolls at the strip edge position, raising the roll temperature outside of the strip width, which extends the rolls’ thermal camber to provide improved control of the strip edge shape. This reduces the chance of strip breakage caused by tight strip edges. Additionally, the inductor system consumes less energy during operation when compared to similar products in the market, such as hot edge sprays – at a lower installation cost.
Improved product quality
During rolling, coolant sprays are applied to manage the temperature of the roll, thus maintaining product flatness. However, during high-speed rolling, a drop in thermal camber can occur at the strip edge, creating a “cool spot” on the roll at the strip edge. At this point along the roll, the cooling spray has no effect on product flatness, leading to tight edge issues.
The hot edge inductor addresses this problem by providing additional heat to the work roll at the strip edge position, expanding the roll and alleviating tight edges. This leads to improved control of the strip edge shape, enabling customers to achieve their key objectives of product quality and maximum cold mill capacity, thereby allowing Hulamin to meet the market demand in can packaging.
Largest semi-fabricator in sub-Saharan Africa
Hulamin is the largest aluminum semi-fabricator in South Africa supplying customers across Africa and the world with aluminum sheet, plate, and foil products, serving demanding markets such as packaging, automotive, transport, building, electrical, and general engineering. The company exports more than 60 percent of its sales to global customers and operates three businesses: rolled products, extrusions, and containers.
Key facts: Scope of Supply
The project scope includes the supply of the hot edge inductor system, comprising of:
- Induction heating heads
- Heater power control cabinet
- Exit feed table
- Hydraulic cylinders with integrated position transducers
- Hydraulic valve stand
- Inductor head cooling system
- Position control system
Hydraulic cylinders are provided to position induction heating heads close to the roll surface, thus overcoming thermal camber, which leads to tight edge issues generated during high-speed rolling.
Contact information
E-mail: info@primetals-ru.com
Legal address: 10 Gilyarovskogo str., bld. 1, 4th floor, Moscow, 129090
Physical address of the Moscow office: 10 Gilyarovskogo str., bld. 1, 4th floor, Moscow, 129090
Moscow office phone #: +7 (495) 114-55-18
Physical address of the Ekaterinburg office: Karl Liebknecht str., bld. 4, Ekaterinburg, 620075
Ekaterinburg office phone #: +7 (343) 379-23-95